by Isaac Sorensen, CSI, Russ Snow, CSP, CTR, BSS, LEED AP, Scott Wolff, CSI, CDT, BEC, Conleigh Bauer, CSI, Stacey Bogdanow, CTR, Taylor Wodzinski, Patrick Raney, CSI, ICRI, and Roger Smith, CSI, ICRI
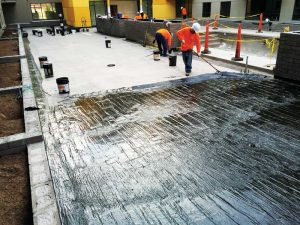
After centuries of use, fluid-applied waterproofing continues to evolve as the primary method of structural waterproofing. According to Grand View Research, fluid-applied waterproofing is predicted to be a $37-38 billion market by 2025. Historically, humans have used variations of liquid membranes to waterproof their structures since hunters and gatherers used large leaves and tree sap to protect their excess grain from moisture. In the Neolithic era, boats were sealed with bitumen emulsion from peat bogs to prevent water from deteriorating the wood. Ancient Egyptians perfected bitumen emulsion to seal and protect walls from the Nile River. With all the technological advancements over the years, it is remarkable these base chemistries are still used.
Fluid-applied waterproofing materials offer certain advantages over self-adhered sheet membranes, primarily the ease of installation, simplified detailing, and cost efficiency. Many challenges associated with sheet membrane waterproofing systems, such as ‘fish mouths,’ uneven seams, difficult end lapping, and complexity of installing a straight flat sheet on a polygonal structure, are eliminated in a fluid-applied system. With liquid membranes, minor substrate imperfections, small gaps, and irregularities are easily addressed. The seamless, monolithic quality of a liquid membrane reduces the concern of failures at joints, laps, seams, and changes in plane. The elastomeric properties of a fully adhered, fluid-applied system will accommodate minor settling and structural movements due to temperature and humidity changes.
Whether sprayed, rolled, or troweled on, liquid membranes reduce waterproofing installation costs by eliminating time and labor associated with substrate priming, taping, and rolling seams, and measuring and cutting large prefabricated sheets. While many variables, such as the skill of the installer and the specific site conditions, influence the final installation cost, some estimators report a labor cost reduction of up to 60 percent by using a fluid-applied membrane over a traditional sheet-applied membrane. When it comes to surface preparation, although a fluid-applied membrane is a little more forgiving with regards to surface profile, proper preparation is still The installation schedule is similarly dependent on many variables, but a sheet-applied membrane system usually requires an estimated two to three times the installation time compared to a spray-applied waterproofing membrane system. The ability of cold fluid-applied membranes to be installed over ‘green’ concrete is another advantage in regard to the ever-shortening construction schedule.
Liquid-applied waterproofing materials
Liquid-applied waterproofing can be categorized into bituminous materials, coal tar, and polymeric materials. Bituminous binders result from the petroleum refining process and are commonly known as ‘asphaltic’ or ‘asphalts’. The earliest discovery of bitumen dates back thousands of years to Europe and Africa. Despite being inherently combustible, bitumen is a sticky, naturally occurring and adhering, semi-solid, and innately hydrophobic material, highly suited for use in waterproofing membranes. With all of the technology for below-grade waterproofing, the use of bituminous membranes is still popular, and can be accomplished using a large array of accessory materials. It is imperative adequate research is done with regards to any materials that it will come into contact with these membranes to ensure both chemical and adhesive compatibility.
First discovered in the mid-1660s, coal tar is a byproduct of coke and coal gas production. It was commonly used in roads, sidewalks, and the preservation of railroad ties by 1865. The combination of coal tar and organic saturated felts became one of the earliest roof membranes. However, coal tar was limited to low-slope roofs due its low viscosity. Coal tar is also highly susceptible to ultraviolet (UV) degradation, often resulting in severe craze cracking in its cured form. For better UV stability, various resins, epoxies, and other materials were added as UV-resistant enhancers, including aluminum flakes. Despite the challenges, coal tar maintained a nearly 100-year popularity until the product was discovered to be carcinogenic. State and local volatile organic compound (VOC) restrictions banned its use for roofing applications and significantly reduced its use today. One other consideration is this material is also combustible, another limitation restricting its use.
Polymerics require complex formulations to cure to a solid membrane material. Most polymer technologies are highly processed and consequently more expensive than asphalt or coal tar. Polymer technologies are also less hydrophobic and have inherently lower viscosity than asphalt or coal tar. However, the installation advantages to these technologies continue to encourage their use in the field. These polymer technologies include polyurethane, acrylic (polymethyl methacrylate [PMMA]), silicone, acrylic urethane hybridization (polyurethane methacrylate [PUMA]), and silicone urethane (SPUR). As these materials are not produced from crude oil, they are deemed to be a more sustainable building material when compared with bituminous membranes.
Bituminous membranes
In the early 1900s, cold fluid-applied membranes were developed primarily for the maintenance of roadways and dust mitigation. Cold-applied membranes include cutbacks, cold-process, and emulsions, which refer to slight variations in the chemistry.
An asphalt cutback is simply heavy-grade asphalt thinned with lighter grade petroleum solvent to provide a higher viscosity and easier workability. Solvent-based cutbacks are rarely used today, and the term cutback has essentially vanished from product literature. These products are still available but limited by state and local codes due to their flammability, odor, and higher VOC content. These limitations often outweigh the benefits of cooler weather application and styrene butadiene styrene (SBS) membrane compatibility.