by Chris Bennett, CSI, iSCS, CDT, Bill Dubois, AIA, CSI, CCS, John Guill, FCSI, AIA, IIBEC, SCIP, CCS, CCCA, Keith Robinson, RSW, FCSC, FCSI, Rae Taylor, PhD, and Jonathan Ware, AIA, LEED AP, LEED CxA
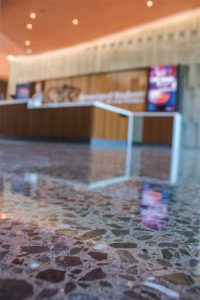
Concrete slab surfaces have voids. They can be big or small. Voids might come in the form of visible cracks, a dislodged piece of aggregate, or much smaller spaces on the micro or nano scale. Voids might be produced later in a slab’s life due to floor traffic over a curled joint. When joints break down, visible voids are created, wear and tear at uneven portions of the slab is increased, and additional maintenance costs are incurred. These voids are the weak points that reduce a slab’s life cycle and increase permeability—thereby allowing dirt and abrasives to quickly wear away the surface—as well as the probability to be negatively affected by moisture, contaminants, and other negative traits that facility owners do not want for their exposed concrete walkway surfaces.
For existing concrete, one can either deal with these voids through coating (sometimes referred to as sealing) or by refining and changing the surface via polishing. Unfortunately, not enough members of the project team are fluent in differentiating between the coating products of Division 09 and the cementitious products of Division 03. The terms “coatings” and “polishing” are often confused, especially when it comes to the many clear coating technologies available.
Coatings
There are many types of concrete coatings from polyuria, polyaspartic, and polyurethane to epoxy and acrylic. Concrete coating types are many. Polyurethane usually does not bond well to concrete, but epoxies do. This means these coating technologies are often used together. Epoxies fill voids and polyurethane coatings are used as the finish coat to establish slip-resistive, durable, and aesthetically pleasing floors.
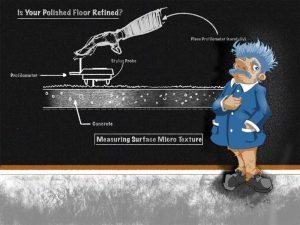
Water-based coatings, such as acrylics, are quick and easy to apply, but require frequent maintenance and repairs, making them a less sustainable option when compared to solvent-based coatings. The latter generally lasts longer, but can turn yellow or amber when exposed to ultraviolet (UV) light (in the case of epoxies) or with oxygen reactions to the solvent (in the case of acrylics, polyaspartic, and polyurethane). Two- and single-part products containing no solvents have become more readily available in recent years as technologies advance to combine various hardening and adhesive properties, which reduces many of the concerns for appearance retention.
Siloxane and silane coatings are derived from the silicon molecule and can penetrate deeper under the surface than other coatings. They are applied by dipping, spinning, or spraying. The downside of these types of coating is their lack of chemical resistance and the need for reapplications. Floor coatings with high solid content may need to be avoided in certain industrial and commercial applications, as they will easily become tarnished from fork lift and foot traffic.
Some coatings can enjoy high gloss if burnished. However, this can cause confusion with polished concrete installations. Gloss benchmarks for coatings include distinctness of image (DOI), similar to the auto coatings industry. As coatings tend to be film-forming by nature, maintaining higher traction levels, and thus a higher coefficient of friction (COF), can be more difficult. Epoxy coatings, including thin-mil coated floors made by resin-tool transfer, can decrease COF. Anti-slip broadcast agents may need to be used to ensure safer walking surfaces. With slips, trips, and falls listed as one of the “fatal four” injuries, and 67 percent of those happening on the same level, an appropriate COF is an important component to user safety.
Densifiers
Using a densifier does not mean the floor is being polished. It is all about application. A concrete densifying agent can be employed in either coated floor systems or concrete polishing. They can be applied like a shell coating to the top of a slab or processed into a floor to aid in refinement and strengthen inside the slab. Densifiers typically do not enhance substrate color, but can produce some sheen as a coating or with polishing. Densifier performance is based on a number of factors, including pH, percentages of solids, molecule size, and application.
There are two basic types of densifiers—silicate and silica. Examples of silicates are sodium, potassium, lithium silicates, or magnesium flourosilicates. Some silicate technologies have been around since the time the Model T was in production, but still have some uses in modern construction as a floor coating. In the presence of moisture, densifiers become chemically reactive with calcium hydroxide (CH) to produce calcium silicate hydrate (C-S-H). Silica densifiers are a newer, more reactive type. Some of these products are referred to as colloidal, which describes the suspended state of silica.