by Dwight D. Benoy, PE, Pamela Jergenson, CCS, CCCA, BECxP, CxA+BE, and Gary C. Patrick, AIA, RRC, CSI
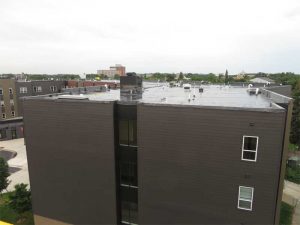
When three separate wood-frame structures in the northern United States showed evidence of possible moisture infiltration in the roof areas, an independent architectural/engineering consulting firm was called in to confirm the issue was present, determine the amount of damage, find the source, and design solutions. All three buildings had been built within the last 10 years, and shared similar design characteristics, with commercial space on the first floor and apartments on the upper levels. When all three assessments had uncovered premature failures to some structural components of the roof assemblies as a result of accumulated moisture in the truss space, a thorough investigation into the source had to be conducted.
Background
All three buildings had similar non-ventilated, low-slope roof assemblies utilizing wood trusses with a polyethylene vapor retarder on the bottom of the trusses covered with a gypsum ceiling. Blown-in fiberglass or cellulose insulation filled the truss space from the ceiling to the bottom of the roof deck on all three buildings. Oriented strand board (OSB) of 13-mm (1/2-in.) thickness was installed over the trusses as the roof deck. Rigid board insulation was installed over the OSB, followed by the roof membrane, which was a gravel-surfaced built-up roof in one case, a ballasted ethylene propylene diene terpolymer (EPDM) single-ply membrane on another, and a mechanically fastened thermoplastic polyolefin (TPO) single-ply membrane on the third.
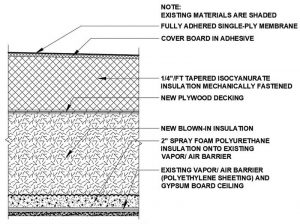
Images courtesy Inspec
Water intrusion was not evident in any of the buildings. A survey of the roof surfaces showed they were in good condition. Occupants in two of the buildings reported mold issues, which led to further investigation. Maintenance people walked on the roof of the third building and discovered soft spots, which turned out to be locations where the OSB roof deck had lost its structural integrity due to moisture degradation.
It was apparent moisture-laden air had migrated into the truss space of all three buildings and condensed in the upper reaches of the roof assemblies. This resulted in excessive moisture buildup, mold, and rot of the OSB structural roof deck and structural trusses in a substantial portion of the roof area.
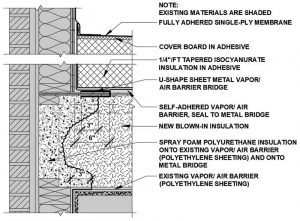
Ideally, the vapor retarder should act to minimize the amount of moisture vapor from the interior of the buildings getting into this space. In the northern climate where these projects were located, the vapor drive in the winter is mainly from the warm interior to the cold exterior. The warm interior air carries moisture vapor that will condense on surfaces below the dewpoint, the temperature at which condensation can occur.
The investigations found many bypasses in the vapor retarder that would allow the warm, moist interior air to migrate into the truss space. The party walls between apartment units, which were a double-stud wall construction, interrupted the continuity of the vapor retarder.
Similarly, all interior partition walls resulted in a discontinuity in the vapor retarder at the ceiling. This was exacerbated by the penetrations through the top plate of the wall by plumbing stacks and wiring. Penetrations through the ceiling, such as sprinkler heads and electrical boxes for light fixtures, were also found unsealed to the vapor retarder.
Two of the buildings had ducts from bathroom and dryer vents running through the truss space. Some of these ducts were not well-sealed at the joints, thereby introducing moist air directly into a space with a potential for condensation.