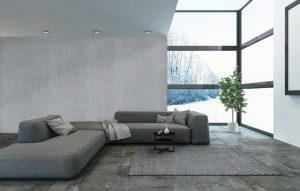
Outdoor lifestyle is crucial to commercial buildings
In the mid-20th century, drywall swept through the U.S. construction industry and made the interior plastering trade outdated. For more than six decades, the last step in installing drywall has been a process of spackling and sanding to smooth over heads of fasteners and joints between the wall panels. While this method of finishing has changed little during that time, the cost of labor has increased, more so than the cost of materials. As a result, the labor-intensive and dirty process of finishing ready-to-paint drywall has gotten much more expensive.
As the construction industry heads into another year with a shortage of qualified labor, the upward trend in labor costs is expected to continue, and the quality of workmanship is likely to decline as less-qualified labor must be hired. It is an appropriate time to consider less labor-intensive options for wall finishing.
A technique widely used in Europe can eliminate common defects on both walls and ceilings, and offers a cleaner, faster, more efficient finishing process. Instead of applying three coats of joint compound to smooth a wall, glass fiber textile is adhered to the entire drywall surface. It can be applied over a very low-level drywall finish, saving time and labor, and achieving the equivalent of the highest level of drywall finish at lower costs. The application procedure is fast, easy, and requires little training to master. Walls and ceilings are finished and ready to paint faster.
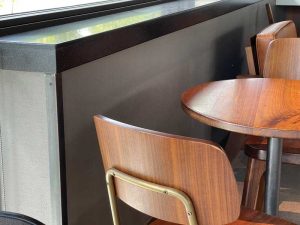
Glass fabric-clad walls have numerous performance characteristics which make them an improvement over bare drywall, and they are available in a broad range of engaging aesthetic options that go far beyond smooth. This method of wall finishing has been common in Europe for decades, where hundreds of millions of square meters are applied to walls and ceilings every year. It has only recently emerged in the U.S. Glass fiber textile walls have been applied in numerous Starbucks locations in at least six states (Florida, Mississippi, Alabama, Louisiana, Massachusetts, and Nevada). They provide a damage-resistant solution in high traffic locations such as seating areas, corridors leading to bathrooms, and in the retail store, while also creating an attractive appearance.
Drywall finishing standards
A smooth wall, painted or papered, is the norm for interiors in the U.S. Walls featuring wood paneling, exposed brick, or glass are also common, but they are still special finishes. The baseline is a hard, smooth, opaque painted wall. It is often made of drywall—gypsum board panels or, less frequently, magnesium oxide panels. These panels have smooth surfaces. To render the panel-to-panel transitions just as smooth, a system of taping and smoothing with joint compound has evolved, with standards for how to apply it. For instance, GA-216 Application and Finishing of Gypsum Panel Products and GA-214 Recommended Levels of Finish for Gypsum Board, Glass Mat and Fiber‐Reinforced Gypsum Panels, published by the Gypsum Association detail how to install and finish drywall. Much of this is also incorporated into ASTM C480 Standard Specification for Application and Finishing of Gypsum Board.
GA-214 lays out five levels of finish using tape and joint compound (mud), with increasing degrees of smoothness appropriate to different types of applications, from the simple Level 1 for walls that will generally be concealed from public view to Level 4 and Level 5 for painted and wall-papered interiors. A modified version of the levels of finish is included in ASTM C480 as Appendix X8.
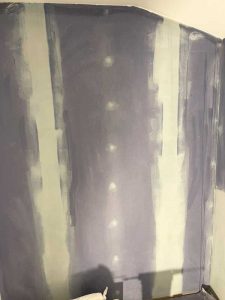
These finishes can be thought of as the five levels of smoothness, or as levels of allowable imperfection. Level 4 is intended for appearance areas where smooth walls are decorated with flat paints, light texture coatings, non‐continuous textures, or wallcoverings. Level 4 is the minimum acceptable finish for painting or for wall coverings that will reveal imperfections in substrate smoothness. The standard requires three coats of joint compound on the joints and fastener heads, each wider than the previous coat, and each sanded in between coats. The third coat on the joints must be spread 152 mm (6 in.) from the joint center on each side. On a 1219-mm (48-in.) wide panel, joint compound will cover 25 percent of the board surface. The three coats over the fastener heads and accessories effectively increases the covered area to about 30 to 35 percent. Each layer must be allowed time to set or dry, and then sanded smooth. After three coats, a layer of drywall primer is necessary, prior to painting, primer, and finish coats.