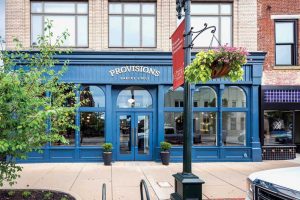
By Fiona Levin-Smith
Powder coatings have been around for a long time. Most people know them as tough, beautiful, protective coatings, used on metal substrates
and available in many colors. However, what many people
do not realize is there are different types of powder coatings with different performance capabilities.
Architectural grade powders are performance coatings designed specifically for architectural applications. As such, they have excellent technical capability, display great weatherability, color and gloss retention, corrosion and humidity resistance—while delivering a beautiful finish. A factory-applied finish, powder coatings are electrostatically applied and cured in an oven where heat creates a chemical reaction to turn it from a powder into a protective film.
These performance coatings offer a variety of colors and effects, alongside the same types of warranties as liquid coatings, but with an improved sustainability footprint.
Manufacturing and application
Essentially, a powder coating is a type of paint. Instead of relying on solvents or water, powder coatings are typically made by combining measured amounts of raw materials, which include resins, pigments, crosslinkers, and more, into a mixer. Once the ingredients are combined, the mixture is melt-mixed in an extruder and then cooled and broken into chips. The thin, brittle chips are then milled and sieved to make a fine powder.
In the architectural world, powder is usually applied to metal substrates such as aluminum or steel. Ensuring those metal substrates receive the correct pretreatment is an important part of the coating process and in achieving performance goals. The pretreatment options differ between aluminum—which is often a chrome or non-chrome conversion coating—and steel, where etching and blasting is also an option.
Once the metals have been properly pretreated, they are ready to be coated. Applying the powder is also slightly different from what one might think of when a traditional “paint” comes to mind. The most common form of application in the U.S. is through electrostatic spray application. To apply the powder, the metal parts, whether its extrusion for curtain wall, window frames or doors, are hung on a conveyor and the parts are grounded.1
The powder is placed in a hopper, usually a sealed stainless-steel container which has a perforated plastic membrane on the bottom. This membrane has tiny holes in it that allow compressed air to enter the container and constantly ‘fluff’ the powder to showcase flows around and inside the hopper. This does not turn the powder into a liquid, but it does make it behave like a liquid, so the powder can then be pumped up from the hopper, through a hose, and into a powder gun.