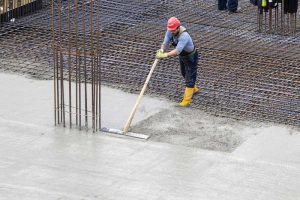
By Julie Holmquist, Ash Hasania, and Lisa Marston
In construction, service life demands are increasingly rising. It is becoming more common to receive design requests for bridges, high-rises, and other concrete structures with service lives of 100 or 150 years.
How is an engineer to keep up with these demands while staying within a limited budget? If funding is plentiful, what additional steps can be taken to maximize reinforced concrete durability? Corrosion inhibiting admixtures can be an important piece to this puzzle, but their selection should be made while carefully understanding the characteristics of each type. This article discusses some key considerations engineers should make first when choosing whether or not to use a corrosion inhibiting admixture and subsequently choosing which admixture to specify.
Why is concrete corrosion a concern?
Corrosion protection has a huge impact on the service life of reinforced concrete and should be considered for any concrete structure meant to last more than 10 years. Concrete creates a naturally protective environment for reinforcing metal because of its high pH. This alkaline environment initially inhibits corrosion of embedded rebar. However, as time goes on, the concrete reacts with atmospheric CO2 and ultimately replaces calcium hydroxide (Ca[OH]2) with calcium carbonate (CaCO₃), which lowers the pH of the concrete so the rebar is no longer protected. This process is called carbonation and typically occurs at a rate of about 1 mm (0.039 in.) per year.1 It therefore may not reach the depth of the rebar for several decades. However, some environments, such as industrial parks, may have higher CO2 levels that accelerate carbonation and shorten time to corrosion.
While carbonation can play a role in concrete corrosion, chlorides are often the foremost concern because they can incite corrosion even before carbonation sets in. Chlorides from sea spray, deicing salts, or saline groundwater leach in through concrete pores and combine with moisture to create an electrolyte that speeds up rebar corrosion rates. When concrete begins to crack due to physical damage or freeze-thaw cycles, matters get worse because the chlorides have a new path that makes it even easier for them to reach the surface of the steel.
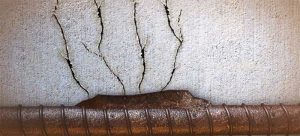
Once corrosion initiates, it starts a chemical reaction in which the iron in the steel reinforcement oxidizes. The resulting iron oxides, or rust, represent metal loss on the rebar. They also have a higher volume than the original reinforcing steel. This “swelling” of corrosion products puts pressure on the overlying concrete, leading to cracking and spalling, which exposes the reinforcement to more corrosives. The vicious cycle continues deteriorating the structure until replacement or proper repairs take place.
Aside from the safety concerns of an unsound structure, the economic and environmental costs are chief concerns because of the high investment in energy-intensive raw materials needed to build a new structure. Putting preventative measures in place to delay the time to corrosion and reduce the rate of corrosion that has already started is therefore one of the key strategies an engineer can take in designing a structure to last longer.