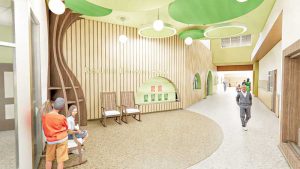
By Chris Bennett, iSCS, CDT and Keith Robinson, FCSC, FCSI, RSW, LEED AP
Just as successful specifications enjoy the four attributes of being clear, concise, correct, and complete, concrete also has four steps that are crucial to its success. Those steps are: mix design, consolidation, finishing, and curing. If the four steps work together in concert, the outcome is low porosity, strong, sustainable concrete. However, make changes to one step and not judicious adjustments to the others, and one will find themselves out of step, over budget, and in trouble.
CSA A23.1 states it is the general contractor or construction management team’s responsibility to prepare a “Concrete Plan” that defines the expected roles and responsibilities of all parties contributing to the quality of concrete, including mix design, consolidating, finishing and curing. However, it is up to the entire team to understand and execute this process together, employing performance-driven methods, to successfully arrive at the design intent.
Mix design
The first step, mix design, is the process of determining the ideal proportions of cement, water, aggregates, and additives to produce concrete that meets a project’s specific requirements. ASTM C 125, Standard Definition of Terms Relating to Concrete and Concrete Aggregates, explains concrete is a composite of cement and embedded fragments of aggregate (rock and sand). When combined with water, the cement binds the materials together, creating concrete. The quality and properties of raw materials, including supplementary cementitious materials (SCMs), can vary significantly, affecting the consistency and strength of the concrete mix. The mix design is critical for targeting desired strength, workability, and other properties.
Then the mix design must be carefully adjusted to meet site-specific conditions, such as temperature, humidity, and wind. ASTM C94/C94M, Standard Specification for Ready-Mixed Concrete, provides basic guidance on mixing concrete thoroughly to ensure uniformity and workability. A well-designed mix is essential to ensure the longevity and strength of the structure. It is important to bear in mind that new types of concrete mixes, such as those intended to reduce carbon dioxide emissions, may fundamentally change the behavior of concrete (i.e. water demands, workability, set times, etc.) and must be handled differently than traditional approaches to avoid dry-shrinkage, deflection, and other potential problems.
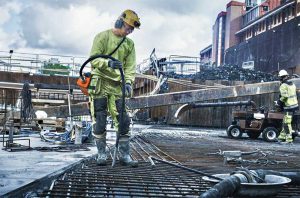
Consolidation
Consolidation (also called compaction) is the process of packing and molding the concrete within the forms and other structural elements, removing any trapped air pockets that can weaken the concrete’s overall strength. Consolidation is critical because elimination of any gaps or voids in the concrete leads to more uniform strength and higher density. Improper consolidation results in a weaker concrete structure that can fail. ASTM C138/C138M, Standard Test Method for Density (Unit Weight), Yield, and Air Content (Gravimetric) of Concrete, provides instructions for the consolidation needed to produce concrete that can withstand loads and stresses and limit cracks, defects, and avoid shorter lifecycles.