Monica Schultes
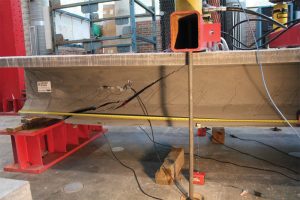
While concrete has been around in some form for thousands of years, the newest iteration, ultra-high-performance concrete (UHPC), is creating a stir. UHPC has been used to build bridges and architectural façades around the world. However, in the United States, UHPC’s use has been limited to-date—its widest use is in joints and connections.
Ongoing research and development efforts are changing that. This technology can have a big impact and be adopted in both building and transportation construction. The U.S. precast concrete industry is well-suited to capitalize on the unique performance characteristics of UHPC and has made substantial strides.
UHPC is emerging as a material with the potential to revolutionize segments of the precast concrete industry. With creative designs and new guidelines, UHPC can be cost-competitive on a first-cost basis and provide significant value on a long-term life-cycle cost basis. By taking advantage of its key properties, precast and prestressed UHPC components can transform the industry, with their more efficient use of materials and enhanced long-term performance.
Defining UHPC
UHPC was introduced as ‘reactive powder concrete’ in the early 1990s. It contains many of the same materials as conventional concrete such as cement, supplementary cementitious materials (especially silica fume), sand, and chemical admixtures. However, the materials and proportions are optimized within the mixture to form a dense particle packing matrix. UHPC also differs from conventional concrete by including steel fibers.
The quantity of cementitious materials in UHPC is typically more than double of conventional concrete. Instead of referring to water-cement (w/c) ratios, these special blends refer to water-binder ratios (w/b), which are often less than 0.2. The dense particle packing, combined with the extremely low w/b, creates a highly refined microstructure providing exceptional strength and durability.
There is no standard definition of UHPC, but it typically has compressive strengths of more than 119,969 kPa (17,400 psi), with some able to achieve strengths up to 206,843 kPa (30,000 psi). However, compressive strength is not the most significant enhancement. The key difference between UHPC and other concrete is its high tensile strength and durability, due to the combination of the sophisticated microstructure and the use of steel fibers.
UHPC’s potential
The precast concrete industry has potential to improve its product offering by using UHPC, as it will enable the production of precast concrete components that are thinner and lighter, yet capable of longer spans with less reinforcing. UHPC is more than just new mixture proportions.
“If we dwell only on the material side then we will keep filling joints with UHPC,” said Maher Tadros, founder of eConstruct USA LLC, a Nebraska-based structural engineering firm. “The real benefit comes from our engineers and designers who are creating new products. That is where we start the revolution.”
Two conditions must be met for UHPC to see widespread implementation. First, precast concrete plants must be able to produce it reliably and cost-effectively. Second, design of new components and systems capitalizing on its unique performance characteristics must be developed.
Research team

The Precast/Prestressed Concrete Institute (PCI) is funding an applied research project led by eConstruct USA LLC in joint venture with Wiss, Janney, Elstner (WJE) Associates Inc., the University of Nebraska–Lincoln, the Constructed Facilities Laboratory at North Carolina State University, and Louisiana Tech University.
PCI’s primary goals are to create cost-effective UHPC using local materials and develop design guidelines for optimized long-span structural members for buildings and bridges.
“While UHPC has been used successfully all over the world, the main drawback in the United States is the cost and the lack of nonproprietary mix designs,” said Greg Force, PCI Research and Development Council chair. Another missing component, he said, “is the means for acceptance by the general design and construction community.”
The research team is not testing theoretical models, but rather the rapid implementation of UHPC in actual structural members for real projects. To emphasize the point, Tadros refers to bridges built in Iowa more than 10 years ago that were not repeated because the premium cost was funded by the federal government.
“We cannot afford to sit around and wait for one project in a while to come along,” said Tadros.
The research addresses precast and prestressed concrete members that can span up to 18 m (60 ft) for buildings and 76 m (250 ft) for bridges. The building beams are voided inverted tee beams and the joists are thin-walled voided slabs with stem openings (block-outs) to allow utility placement. All products are pretensioned in the longitudinal direction.