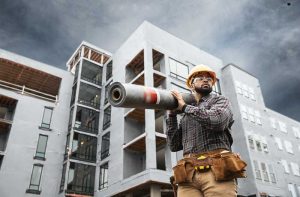
by Bijan Mansouri
The importance of moisture management cannot be overstated. Water intrusion comes with the potential for moisture-related issues like mold and rot in the building envelope. Since the elusive ‘waterproof wall’ is yet to be invented, specifiers must turn their attention to effective moisture management strategies to best protect wall assemblies. Weather-resistant barriers (WRBs), also known as building wraps or housewraps, are one of the best building materials for controlling water, either through blocking rain from entering the wall cavity, allowing moisture vapor to move and escape the wall cavity, or draining bulk water away from the wall assembly.
Moisture management strategies impact all stakeholders in the design and building process. Specifiers want to be certain the material’s moisture management properties will support the performance of the envelope throughout the building’s lifespan, contractors need an installer-friendly and field-tested WRB, and architects should be certain cladding options will be compatible with the barrier.
Role of WRB in managing moisture
The main role of WRB is to protect the building envelope from bulk water, wind-driven rain, and water vapor. How does a WRB work against all three forms of intrusion? There are three primary defense mechanisms:
- water holdout for bulk water;
- drainability for rain penetration; and
- proper permanence or breathability for water vapor.
Water holdout for bulk water
As its most basic function, a WRB must hold out liquid water. A high-performance building wrap will be able to pass both ‘water ponding’ tests, which measure a building wrap’s resistance to a pond of 25-mm (1-in.) water over two hours, and a more stringent hydrostatic pressure test where the material is subjected to a pressurized column of water for five hours.
Drainability
A WRB is an effective material for keeping the wall assembly dry and reducing the potential for moisture damage. As the trend for tighter building assemblies continues to grow, building wraps have taken on a new function—removing trapped water from the wall assembly. The very latest innovations in housewrap technology are taking this moisture removal function one step further by incorporating drainage capabilities.
The drainage efficiency of a building wrap is generally tested in accordance with ASTM E2273, Standard Test Method for Determining the Drainage Efficiency of Exterior Insulation and Finish Systems (EIFS) Clad Wall Assemblies. In simple terms, this test involves spraying water on a wall assembly and measuring its collection over time. However, given the diversity of drainable building wraps on the market, the rate at which bulk water is drained varies a lot.
Today’s building wraps integrate drainage gaps into the material itself through creping, embossing, weaving, or filament spacers. These new technologies eliminate the need for furring strips, thereby helping to reduce material costs and streamline installation.
These new drainable building wraps meet all current code requirements for drainage efficiency (ASTM E2273) without sacrificing any of the durability and ease-of-installation benefits builders and contractors have come to expect from premium building wraps, since they essentially handle and install the same. They are also vapor permeable, so moisture will not get trapped in the wall assembly and cause mold or rot issues.
Permanence
A WRB must breathe to prevent moisture vapor from getting trapped in the wall cavity. Permeability measures the amount of vapor transmission a building wrap will allow over a period of time. For a product to be considered a WRB and not a vapor retarder, International Code Council (ICC) mandates the permeance rating must be higher than 5 perms. However, permeability can be achieved in a myriad of ways. For example, many low-grade housewraps achieve high perm ratings with mechanically punched perforations in the membrane. Conversely, more advanced non-perforated housewraps offer greater moisture vapor transmission (higher perms) than their perforated counterparts and are more effective at preventing the movement of bulk water.
In the paper, “Inward Drive – Outward Drying,” building scientist, Joseph Lstiburek recommends specifiers aim for the “sweet spot” of 10 to 20 perms to achieve the desired balance of moisture protection and breathability. Achieving the optimal perm rating ensures that while water is prevented from entering the wall cavity, ideal levels of moisture vapor are still allowed to escape. Too high, he writes, and the moisture driven out of the back side of the reservoir cladding into the airspace will blow through the layer and the permeable sheathing and into the wall cavity. Too low, and the outward drying potential of the cavity is compromised. Thankfully, advances in building wrap technology are adapting to meet this need.
Material selection
An array of materials can be used as a WRB, but they are all not equal. When evaluating the potential effectiveness of a WRB, durability and the balance of holdout and permeability are critical factors.
Plastic building wraps
Plastic, nonwoven building wraps have been the most popular WRB for the last 40 years. Their effectiveness is rooted in their ability to shut out air and water, while simultaneously allowing walls to breathe. Typically made from polyethylene (PE) or polypropylene (PP) fabrics, synthetic housewraps are both lightweight and easy to install. In addition to boasting high-performance air and water holdout, plastic building wraps offer exceptional moisture vapor transmission, ultraviolet (UV) stability, and even increase the energy efficiency of the building.
When it comes to building wrap, ICC tests durability on two primary indicators: tensile strength and tear resistance. These factors are critical because the wrap needs to be able to stand up to the handling and installation process without compromising its water resistance.
Tear resistance, as measured by trapezoidal tear tests (ASTM D1117, Standard Guide For Evaluating Nonwoven Fabrics), is a good measure for predicting a building wrap’s ability to withstand the rigors of the jobsite and also to stay on the wall after installation. ‘In-plane’ is the best measurement of tear resistance. The trapezoid tear test, the best measurement of in-plane tear resistance, takes place when the building wrap is fastened to the wall and is subjected to tearing in the plane of the wall.
Some building wraps make claims about their tensile strength based on ASTM D882, Standard Test Method for Tensile Properties of Thin Plastic Sheeting, which is actually a test for thin plastic sheeting, and not nonwoven fabrics. Since the product is never used in this way, these measurements are not meaningful.
However, the grab tensile measurement is useful. ASTM D5034, Standard Test Method for Breaking Strength and Elongation of Textile Fabrics (Grab Test), tests a 1 x 2-m (4 x 6-ft) material sample and clearly says it is designed for nonwoven fabrics, making it a much better metric for evaluating building wraps.
Installers should also be cognizant of the product’s exposure time to the elements, since frigid temperatures and UV rays can cause cracking. High-performing building wraps have low-temperature resistance and built-in UV protection.