By Anton Dekom
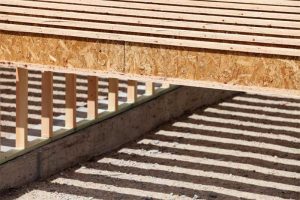
For years, Design for Code Acceptance #3 (DCA3), a document published and maintained by the American Wood Council (AWC), has been the go-to resource for architects working with I-joist assemblies. The document provides designers with a catalogue of non-proprietary, fire-resistance rated I-joist assemblies typically well-known and readily accepted by local building officials.
The wood I-joist (WIJ) assemblies were added to DCA3 in 2001 and were intended to promote the usage of engineered lumber by simplifying the associated design, specification, and permitting processes. Prior to the publication of the WIJ assemblies, architects and engineers had to seek out each I-joist manufacturers’ proprietary literature and fire test documentation to design a custom, non-proprietary assembly or write an open specification. DCA3 made working with I-joists easier by providing a robust set of generic assemblies broadly compatible with most I-joists on the market.
However, in the decades since the WIJ assemblies were first published, revisions to DCA3 have lagged behind developments in the engineered wood industry. Some of the largest I-joist manufacturers have brought products to market that do not comply with DCA3, backed instead by privately commissioned fire test reports based on proprietary assemblies. More specifically, the I-joists which do not comply with DCA3 generally do not meet the minimum dimensional requirements stipulated in the WIJ assemblies. The makers of these joists are major players and cannot simply be excluded from an open specification or generic assembly. The net result is that DCA3 no longer functions as the “one size fits all” standard it once did.
In 2021, designers must once again comb through manufacturer literature and fire test reports1 to design I-joist assemblies compatible with a sufficiently wide-ranging cross section of the I-joist market. As is often the case when referencing multiple proprietary standards, different manufacturers’ specific requirements can conflict with one another. The incompatibility of the various test reports and reference standards makes it difficult to find common ground between generic and proprietary literature.
This article will go into more detail on the shortcomings of both DCA3 and the manufacturer fire tests. The author will demonstrate a few possible avenues for threading the needle between generic and proprietary assemblies and will share some versatile assembly designs aimed at multifamily residential construction: floor and roof assemblies (both one-hour and two-hour rated) that meet code requirements for fire, thermal, and sound. The article will conclude with some thoughts on why the design and specification of I-joist assemblies has become far more complicated than necessary and underscore the continued importance of generic assemblies that work for the whole industry.
I-joist dimensional requirements
Each WIJ assembly included in DCA3 stipulates certain minimum dimensional requirements for the I-joist framing members: overall depth, web width, flange width, and flange depth. In theory, this approach makes it easy for architects and engineers to write open specifications; instead of consulting manufacturer test reports and listing allowable proprietary I-joists (and their compatible companion products), an architect can simply pass on the dimensional requirements in a performance specification, giving the builder on the other end maximum flexibility to competitively bid their lumber package.
Unfortunately, the dimensional constraints listed in DCA3 are no longer in total alignment with the I-joist industry. Of eight I-joist assemblies listed in DCA3, six require a minimum flange depth of 38.1 mm (1.5 in.), a depth that exceeds what is now standard for many manufacturers. Some of the industry’s major players have entry level product lines with flanges as slim as 28.5 mm (1.125 in.) or 31.7 mm (1.25 in.). In many cases these manufacturers also produce I-joists with 38.1 mm (1.5 in.) flange depths, but these are typically heavy-duty joists intended for heavier loads or longer spans. Such joists would be excessive in many applications and typically come at a cost premium.
The remaining assemblies in DCA3 (WIJ-1.3 and WIJ-1.6) stipulate a minimum flange depth of 33.3 mm (1.312 in.), but even this reduced requirement lacks broad compatibility with many I-joist products. The difference may come down to mere sixteenths of an inch, but it is enough to matter when it comes to the applicability of the fire-rated assemblies. Specifications for fire-rated assemblies are always predicated on conformance to the minutest of details, and local code officials can be relied on to nitpick them.
Though it may give cold comfort, it is perhaps a sign of progress that a growing number of I-joists do not meet DCA3’s dimensional prescriptions. When DCA3 was first published, it is likely many I-joists did indeed satisfy all these requirements but, over the years, manufacturers have improved their technologies and found ways to get better performance out of less material. The trend toward smaller flanges is a sign of efficiency — although unfortunately the DCA3 standard has been slow to catch up.
Cavity insulation
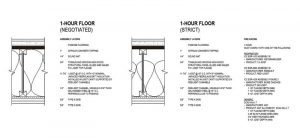
Horizontal I-joist assemblies must accommodate cavity insulation to work in a broad array of applications. On multifamily residential projects, a fully insulated joist cavity is typically necessary to allow the assembly to be used in roof/ceiling applications. For those seeking prescriptive compliance with the International Energy Conservation Code (IECC) (and aiming to insulate the joist cavity rather than provide continuous insulation above the sheathing) R-49 is the minimum required for climate zones 4 (marine) and higher. Achieving this level of performance with cavity insulation generally entails insulating the entire depth of 302 mm (11.875 in.) I-joist roof/ceiling assembly.
Another reason to fully insulate between I-joists is improved acoustic performance in floor and ceiling applications. Floor assemblies for multifamily projects are typically required by International Building Code (IBC) Chapter 12 to meet minimum sound ratings of sound transmission class (STC) 50 and impact insulation class (IIC) 50. It is relatively common for building owners to ask for their floor assemblies to be designed to exceed these code minimums. Adding mass to a floor assembly improves STC ratings (and to a lesser extent, IIC ratings) and is generally an economical way to increase acoustic performance.
Fiberglass insulation, whether blown-in or blanket, is perhaps the most used material for this application. It has been used in residential construction for decades, is commonly available at hardware stores and lumber yards, and is inexpensive.
While it is also possible to insulate the joist cavity with mineral wool batts, the practice is less common. Mineral wool batts typically do not exceed R-38, which means in colder climate zones two batts must be installed between joists to achieve R-49 and costs add up quickly.
Both DCA3 and the proprietary fire test reports offer insulated assemblies utilizing either fiberglass or mineral wool insulation, though not all (WIJ-1.5 and WIJ-1.6) allow full cavity insulation.2 The DCA3 assemblies allowing insulation list the required thicknesses as minimums, but this is not always the case with proprietary I-joist assemblies. Those tested by the Engineered Wood Association (APA) typically match DCA3 closely and stipulate minimum insulation thicknesses, but assemblies tested by the International Code Council Evaluation Service (ICC-ES) are more restrictive and generally do not allow a 305 mm (12 in.) nominal joist bay to be fully insulated.
Given the need for full cavity insulation, the assemblies below will focus largely on finding common ground between WIJ-1.7 and WIJ-2.1 and the proprietary equivalents of these assemblies. WIJ-1.7 and WIJ-2.1 are the two assemblies in DCA3 allowing for fiberglass insulation, and they have direct corollaries in almost every fire evaluation report.
WIJ-1.7 specifies no minimum or maximum insulation requirement whereas the equivalent assemblies in the ICC-ES test reports3 stipulate a maximum of R-30 or 241.3 mm (9.5 in.) The two-hour assemblies are similar; whereas WIJ-2.1 specifies 76.2 mm (3.5 in.) as the minimum amount of fiberglass insulation, the equivalent ICC-ES tested assemblies4 list 76.2 mm as the maximum.
The ICC-ES test reports provide no option for fully insulating a typical 305 mm (12 in.) I-joist assembly. This appears to be a major oversight and complicates our efforts to craft hybrid generic/proprietary assemblies.