by Alana Fossa
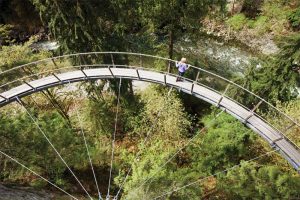
Today’s architects and designers are increasingly looking toward a trendy selection of metals such as stainless steel, aluminum, galvanized steel, painted steel, copper, and weathering steel for commercial building projects. Mixing and matching these metals to achieve a unique combination of colors, textures, patinas, and sheens can add further visual appeal, but such artistic choices require careful consideration when constructing sustainable and low-maintenance exterior structures to last generations. When two different metals are in contact and exposed to moisture containing salts or pollutants, one of the metals can experience accelerated corrosion while the other remains protected. This type of accelerated corrosion between the dissimilar metals negatively impacts the overall corrosion protection of the project and is referred to as galvanic corrosion, bi-metallic corrosion, or dissimilar metal corrosion.
Galvanic corrosion is particularly applicable for projects where hot-dip galvanizing, a process used to apply a metallic coating of zinc and zinc alloys, is specified for the long-term corrosion protection of exterior iron and steel components. Hot-dip galvanized (HDG) steel has a history of providing steel structures with decades of maintenance-free corrosion protection, 100 percent recyclability, low environmental impact, and an industrial aesthetic. These properties continue to make HDG steel a popular and sustainable choice for steel framing, architecturally exposed elements, balcony structures, fencings, railings, fasteners, etc. Since galvanic corrosion can occur at a high rate under certain circumstances, it is important to evaluate the combination of HDG steel with other metals commonly used in building and architecture projects in order to determine whether galvanic corrosion is of concern and how to mitigate it.
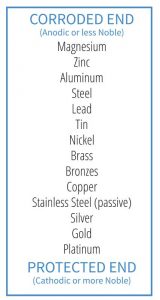
Galvanic corrosion and the galvanic cell
When exposed to a conductive medium such as moisture or saltwater, metals have different electrical potentials. These electrical potentials can be quantified and arranged in order within a particular medium, called a galvanic series. The actual electrical potential values and order of metals vary depending on the specific electrolyte present, but the most common example is the galvanic series of metals in saltwater (Figure 1) (refer ASTM G82-98 [2014], Standard Guide for Development and Use of a Galvanic Series for Predicting Galvanic Corrosion Performance]. Metals such as zinc that is near the top of the galvanic series are more active with a greater negative electrical potential, while metals toward the bottom of the series are more noble or stable. When any two metals of differing potential are combined under specific conditions, a galvanic cell is formed.
In building structures, a galvanic cell (Figure 2) mostly involves direct contact between two different metals exposed to direct moisture or to a humid, marine, or, otherwise, corrosive atmospheric environment. Galvanic cells can also develop upon moisture run-off from one metallic surface to another below. In a galvanic cell, the more active metal gives up electrons to the more noble metal via an electric current. This process results in accelerated corrosion of the more active metal while the more noble metal receiving the electrons is preserved. However, just because dissimilar metals are in contact does not mean galvanic corrosion will occur.