John Trenta
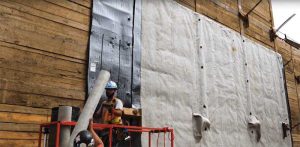
Blindside waterproofing is common in North America, but it is not without its challenges. Handling drainage and sealing penetrations are two critical tasks, among many, that must be addressed to ensure there are no leaks. When designing or specifying blindside conditions, it is best to not jump into it blind. With numerous technologies available today, it is crucial to understand how they all handle real-world applications.
Basics of blindside waterproofing
Waterproofing protects the integrity of a structure and its occupants by forming a barrier to prevent water from entering the building envelope. Blindside waterproofing is more complex than traditional below-grade waterproofing because the process is ‘reversed,’ and waterproofing is installed before the concrete/shotcrete is installed. This method is used when excavation outside of foundation walls is not feasible, such as in urban or high-density areas where a project is close to bordering structures or there is little room to maneuver heavy equipment. The basic process of blindside construction involves the following:
- Excavation is shored with the lagging wall using methods such as soldier pile-and-wood lagging, corrugated sheet piling, soil-nailing, caisson walls, or shotcrete;
- Drainage mat is installed (when applicable);
- Waterproofing is applied to the shoring wall and detailed;
- Structural walls are placed against the waterproofing; and
- Foundation is poured.
Blindside waterproofing technology options
To eliminate potential sources of water ingress, the waterproofing solution must be continuous and have the ability to accommodate normal movements of the structure. Compatibility between the membrane and adjacent components is also important to avoid material failure. Design professionals should be aware of the features and benefits of prominent waterproofing technologies to help identify the best option for their application and to overcome job-specific challenges.
Spray-applied membranes
Spray-applied, liquid membranes provide a monolithic coating for protecting seams and sealing penetrations. The exothermic reaction during concrete cure builds chemical adhesion of the asphaltic membrane to the structure, creating a bonded waterproofing assembly, thus eliminating the potential for lateral water movement. For best results, it is recommended to spray the material onto a flat surface to allow for the correct mil coverage and consistency across the entire substrate.
Bentonite-based sheet membranes
Bentonite sheet membranes have a long history of success due to their controlled mil thickness and multiple components for waterproofing, such as an added high-density polyethylene (HDPE) material. When the bentonite is hydrated, it swells to create an impermeable barrier to water and chemicals. It can also be applied in cold weather and is tough enough to withstand shotcrete applications directly on the face of the membrane. Using this material can be labor intensive though, and requires a specialized trade. For all applications, care needs to be taken to prevent the bentonite from prematurely hydrating, so it needs to be covered with a plastic protection sheet if wet weather is imminent in exposed conditions, or backfilled immediately.
Bituminous sheet membranes
Derived from the roofing industry, asphaltic sheets are a reliable blindside waterproofing option when a flexible material is needed or when applying in cold temperatures. They comprise a modified asphalt-polymer blend with reinforced fiber. Seams are heat-welded together, which can make the application more difficult.
Plastic sheet membranes
For high strength, it is advisable to consider sheet waterproofing membranes made with synthetic materials, such as high-density polyethylene, polymers, and resins. They are impact, chemical- and low-temperature resistant, but they can be more complicated due to the additional detailing involved with penetrations. Their fabric or adhesive layers can provide a mechanical or chemical bond to concrete.
Synthetic-rubber sheet membranes
Synthetic-rubber sheets include flexible and durable materials such as ethylene propylene diene monomer (EPDM). They have excellent water resistance and can withstand ultraviolet (UV) rays and high temperatures. They bond mechanically to concrete, and some product options may have the added benefits of small, self-healing penetrations and self-sealing overlaps.