By Heather (Yario) Rice
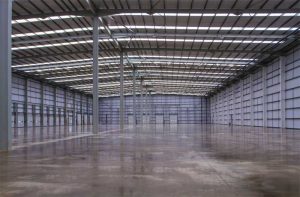
Whether for new construction or renovation, proper subfloor preparation is essential for executing a quality floor installation while extending the life of the flooring. In the last 20 to 30 years, regulations on volatile organic compounds (VOCs) have made buildings safer for occupants; however, these regulations have created new challenges for general contractors, as in the case of moisture vapor related flooring failures.
As the industry’s understanding of moisture emissions has grown, so have the types of solutions used to mitigate the problem. Today, a new category of moisture barriers makes it easier and more cost-effective than ever to properly prepare concrete and protect flooring.
The South Coast Air Quality Management District (SCAQMD) 1168, Adhesive and Sealant Applications was passed in 1989, limiting the amount of VOCs in adhesives, primers, and sealants. Removing solvents from adhesives made them VOC compliant; however, the resulting products were sensitive to moisture vapor in a way the industry has not seen before.
In the author’s observations, prior to the adoption of VOC regulations, moisture-related failures were largely unheard of. They noticed flooring failures began to occur with frequency in the early 2000s. The flooring industry quickly learned moisture vapor emissions were to blame, and they were not only common, but they could result from a wide variety of sources. Slabs, especially on grade, can vary in moisture content. From ground water intrusion to major weather events, the amount of moisture present could vary throughout the slab, increasing and decreasing throughout the life of the building. Slabs that tested with low moisture emissions could still have a failure weeks, months, or years down the road.
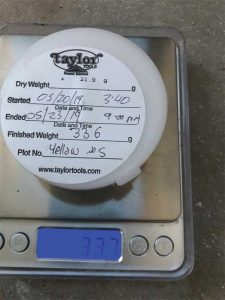
Common construction practices also held the potential to cause moisture issues. The process of burning or hard troweling a slab was used to achieve floor flatness but had the secondary effect of sealing the surface. The application of a cure-and-seal expedited the curing process and sealed the surface to protect it from trade damage. When it came time to install flooring, manufacturers would require the surface of the slab be opened to ensure removal of bond breakers.
Because both processes trapped moisture in the slab, opening the surface allowed water vapor to exit as the relative humidity (RH) of the slab sought equilibrium with the ambient conditions on the jobsite. Not only did this cause condensation to form at the bond of the adhesive to the slab, it also could pull alkalinity from within the slab to the surface, creating a high pH environment. Standard adhesives could handle a pH of up to nine while a freshly opened slab could easily reach a pH of 11 in a short timeframe.
Below the flooring, one of two things would happen: either the adhesive would not dry or adhesive that was dry when the flooring was installed would emulsify. This is where mold, mildew, and other aggravating floor failures would start. As with any emerging issue, preliminary testing and solutions needed to be developed before improvement was possible.