by Rockford Boyer
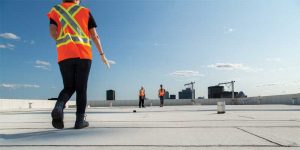
An effective method for a contractor, designer, or manufacturer to visit the inside of a court room is for the building enclosure to develop a leak! A 2011 article in the Journal of the American Institute of Architects revealed 40 percent of issues are caused by moisture. With water vapor-related issues making up almost half of the problems, 70 percent of the litigations interviewed had one issue in common—the roof.
The moisture-related roof issues discussed in the journal could be broken down into the following causes:
• 60 to 70 percent was attributed to poor construction and workmanship;
• 20 to 25 percent was the cause of poor design; and
• the remaining 10 percent was due to material failure.
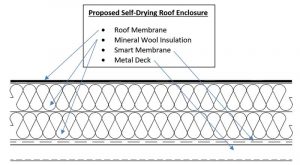
The roof enclosure is one of the most important components of the building. However, the average cost for the roof is approximately two percent of the overall construction cost, as per the article mentioned above. Even if the overall roof cost increases, the chances for a leak-free assembly will almost be impossible if it is badly designed, have badly designed, have poor construction techniques, and lack third-party inspections.
Moisture ingress at the roof level has the potential to negatively affect the durability and resiliency of the enclosure, leading to an increase in operational and maintenance costs. Roof failures and wet roofs also have a large impact on the environment, such as the landfilling of waste materials and increasing carbon emissions with the manufacture and transportation of new products and increased heat flow.
Moisture ingress into the roof enclosure typically occurs through three conditions:
• physical bulk water entry;
• roofing material moisture content (construction moisture and through interior vapor diffusion) and;
• air leakage.
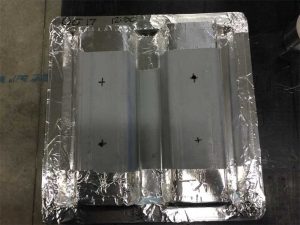
Bulk water leakage through the roofing membrane can be caused by commonly occurring damages from poor workmanship, such as blistering, incomplete laps, membrane punctures, wrinkles, splitting, abuse, and neglect, and inadequate penetration seals and flashing. Roofing materials, specifically moisture-sensitive ones, can become damp or saturated when installed or stored under wet conditions. The installation of an incomplete air and vapor membrane on the metal deck has the potential to allow moist air/vapor to enter the roofing enclosure through the mechanisms of diffusion and convection. Under certain conditions, the difference in pressures can help moisture-laden air and vapor to enter the roof enclosure and condense on the underside of the membrane. Since current construction practices allow the moisture to enter the enclosure, the introduction of a ‘smart’ roof design to promote self-drying will help increase the roof’s durability, resiliency, and thermal performance.