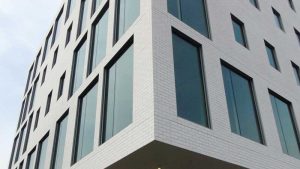
By Donato Pompo
Construction defect litigation is not only doing well, but it is also thriving. There is no shortage of defective construction work and failed projects. Whether it is ceramic tile or natural stone, or any other construction material, construction defects unfortunately are relatively common in projects.
So, what is the problem or problems? Generally, a failure is not due to a single deficiency, but rather due to multiple compounding deficiencies. In the author’s experience, it seems about 95 percent of the time the deficiencies are installer error.
Although there are normally compounding contributing deficiencies, some of them could be the architectural specification due to inaccurate, incomplete, and/or ambiguous specifications. The tile installer relies on the specification to direct them on their scope of their work, on what products to use, and on what methods to use in the installation.
Installers are not architects or engineers, so they should not be expected to make decisions such as the placement and design of movement joints. The installer is expected to follow the manufacturer’s directions and industry standards. The general contractor has oversight responsibilities in not only selecting the subcontractors and orchestrating the sequence of work, but also monitoring the on-site conditions and the subcontractor’s work to some degree relative to the scope of work. Both the subcontractor and general contractor should be submitting requests for information (RFIs) for clarification when there is doubt.
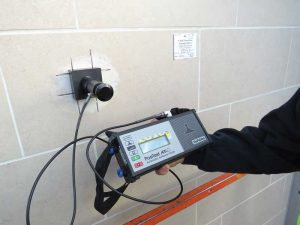
The role of the installer and subcontractor
The focus of deflecting construction defects can be narrowed down to the subcontractor, which could significantly reduce problems and failures. Some examples of common defects could be the installer’s work not meeting the standards or specification for properly adhering the tile and achieving adhesive contact between the back of the tile and its substrate. Another example can be not installing or honoring existing movement joints as per the specifications, standards, or manufacturer’s directions. Another instance can be the waterproofing not being installed correctly or the formation of an inadequate slope on the tile surface or on the underlying membrane in a wet environment. Avoiding excessive tile lippage and other workmanship requirements when tiles are installed is also a common defect.