by Brandon Atwood
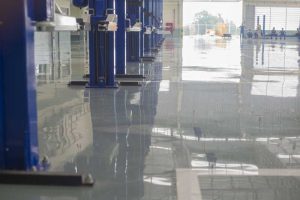
The global anti-static floor market was valued at $3.1 billion in 2018 and is expected to reach $4.09 billion by 2025, according to Crystal Markets Research. It is not just the electronics manufacturing market spurring this growth. As electronics continue to infiltrate the workplace, the applications for electrostatic discharge (ESD) control flooring are expanding. For example, the automated guided vehicles and robots being deployed in e-commerce warehouses can generate large amounts of static electricity when used on standard flooring. ESD control flooring is required to support these technologies.
In large spaces, such as warehouses, data centers, and manufacturing plants, epoxy-based coatings are dominant. Epoxy-based coatings use a conductive material, such as carbon black, tin oxide, or carbon nanotubes mixed with the epoxy coating to create a conductive network across the floor, which is grounded through copper strips.
Epoxy-based coatings represent the most practical and cost-effective flooring option for larger, concrete floors. Installation is straightforward as the coating is rolled on in a multistep process in which the base layer and topcoat are applied over the primed floor. The major challenge with epoxy is that floor aesthetics and performance are difficult to accurately determine until after the floor is installed and fully cured. Post-installation testing is required to ensure the floor has achieved the specified level of dissipation.
Another challenge with epoxy-based coating, particularly prevalent with some commonly used conductive additives, is the floor may turn out to be darker than desired because of the high volume of the required additive. Hot spots may also appear on the floor.
Hot spots occur when the conductive materials within the coating aggregate in certain areas of the floor, thus creating gaps in the network that prevent the floor from dissipating charge to ground. While they can be caused by poor mixing or installation practices, even flooring systems installed by expert, professional installers can experience hot spots and may leave the building owner with an unusable floor while the installer and manufacturer attempt to determine solutions.
This is where understanding relevant standards becomes essential to design professionals. Determining the right level of conductivity for an ESD control floor can have an impact both on its ability to effectively dissipate static charge and on floor aesthetics.
Understanding the ANSI/ESD flooring standard
ESD flooring specifiers deal with a variety of standards and regulations, but for most applications the American National Standards Institute (ANSI)/ESD S20.20, Protection Of Electrical And Electronic Parts, Assemblies And Equipment (Excluding Electrically Initiated Explosive Devices), is the guiding specification, and with good reason. ANSI/ESD S20.20 is maintained by the EOS/ESD Association, which comprises ESD control professionals with extensive experience in the industry and a deep understanding of the nuances of effectively protecting against equipment-damaging static buildup.
The stated purpose of the standard is to outline “the requirements necessary to design, establish, implement, and maintain an ESD control program for…electrical or electronic parts, assemblies, and equipment susceptible to damage by electrostatic discharges greater than or equal to 100 volts human body model (HBM).”
While it is always a good idea for specifiers to understand the entire standard, there are several pertinent points that need to be highlighted.
First, ANSI/ESD S20.20 specifies a program, and not just a flooring specification. The floor is a critical component of meeting the specification, but it must be considered as part of a broader program, including footwear and training.
Next, the ultimate measure of success is not a certain resistance threshold across the floor but to prevent the accumulation of charge leading to a discharge of 100 volts or more from a person. If the flooring can pass a walking voltage test in which discharge at all points is less than 100 volts, the floor is in compliance with ANSI/ESD S20.20.
Finally, ANSI/ESD S20.20 has continued to evolve based on new knowledge and technological changes. The last major revision of the standard was in 2014, and it clarified some important points about resistance levels in ESD flooring. However, as is often the case, practical application of the standard lagged—revisions and resistance levels, as defined in previous versions, continued to be applied.
The right level of conductivity
Generally speaking, flooring that has resistance to ground of 10^6 to 10^9 ohms is considered dissipative rather than conductive, while flooring with resistance less than 10^6 ohms is considered conductive. This distinction was reinforced by previous versions of ANSI/ESD S20.20 and that led to use of one megaohm (1 x 106) as a convenient threshold for specifiers of ESD control flooring.
Many specifiers continue to use this threshold today despite the 2014 revisions to the standard. Instead of specifying 10^6 ohms as a hard target, the goal when specifying ESD flooring is to be on the low end of the static dissipative range while avoiding the static conductive range. Flooring in the 107 to 109 ohm range, when properly installed and supported by other programs, has been shown to meet the charge accumulation requirements of ANSI/ESD S20.20 while avoiding the risks of too much conductivity. The level of conductivity of the floor is largely determined by the amount of conductive additive used in the coating. To get higher conductivity, one would need to use more additive, and that raised the impact of additive on aesthetics and the risk of hot spots. It also increases the likelihood the floor will become too conductive.