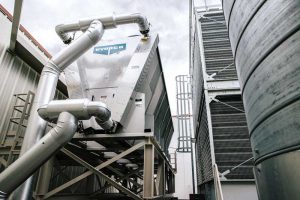
By Mihir Kalyani
The cooling tower is perhaps the most broadly and globally recognized single component of a building cooling system. This has led to the incorrect use of the term “cooling tower” to refer to pieces of equipment that provide both latent and sensible heat transfer in buildings.
When comparing open loop cooling towers to closed-circuit coolers, the heat transfer occurs at different locations. Cooling towers generally have polyvinyl chloride (PVC) fill media where the recirculating water and air come in direct contact. The cooled water then collects in a basin and is pumped directly to a chiller, heat exchanger, etc.
Closed-circuit coolers, also known as fluid coolers, have a heat transfer coil bundle(s) containing the process fluid. Water, and sometimes air, comes in direct contact with the coil, but not the process fluid inside the coil. Therefore, the process fluid remains free of atmospheric contaminants such as dirt and debris.
Cooling towers and closed-circuit coolers are very different pieces of equipment, and while they typically look similar and accomplish the same result, they have distinctive advantages and drawbacks.
A closed-circuit cooler has a larger footprint, heavier operating weight, and is more expensive than the well-known open loop cooling tower (if only the base units are compared). However, fluid coolers have numerous benefits for the end user that are often overlooked.
Proponents of fluid coolers often make the point that, while the units are more expensive than open loop cooling towers, a holistic cost comparison generally shows a similar initial investment. Most cooling equipment manufacturers can provide comparisons between fluid coolers and tower/heat exchanger systems. Traditionally, these comparisons costs fall under the three categories when evaluating the capital investment of a cooling system:
- Equipment costs, such as fluid cooler, cooling tower heat exchangers, pumps, filtration, control panels, etc.
- Rigging, installation, and piping costs such as valves, piping, heat tracing, sensors, and even labor.
- Operation and maintenance costs such as energy consumption, equipment cleaning and maintenance, water treatment, etc.