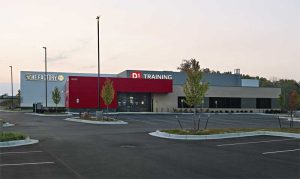
By John Koury and Dean Soll
Options for building skins have improved dramatically over the last 20 years. A deeper understanding of thermal and pressure dynamics between interior and exterior building environments has fueled increasingly complex, multicomponent wall assemblies. However, there is another option when it comes to a thermal barrier, exterior building material: insulated metal panels (IMPs). IMPs are single-component weather barrier wall systems which deliver high-performance value in one integrated, easy-to-install system.
There are multiple versions of insulated metal panels, with a variation on the facing materials, internal insulation material, and panel fabrication methods. This article focuses on foamed-in-place core with fully adhered skins due to their material consistency and high quality. These panels set the standard for this type of building component. The goal for this article is to help specifiers and designers understand the project needs which drive the facing profile, gauge, color, and insulation thickness selections for IMPs, as well as the best applications within the range of IMPs available.
IMPs are a sandwich panel of two metal skins with a foamed-in-place core, fully bonding to the interior surface of the metal faces. The panels are used as part of a steel frame structure, an interior liner panel of a concrete or masonry structure, an unbraced interior partition, or a suspended ceiling. The exterior orientation of the panels can be either vertical or horizontal, each having their own design criteria for the supporting structure.
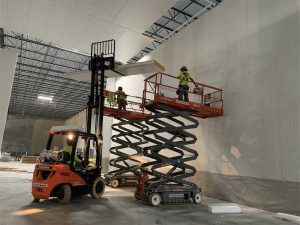
Orientation
Horizontally oriented IMPs run perpendicular to vertical building structures. Often, building column spacing exceeds the required support points. In horizontal IMP installation, cold-formed metal framing, which will likely already be in place for other purposes, can serve as a panel connection point. Functionally, a multicomponent exterior weather barrier, such as an assembly of sheathing, air barrier, exterior insulation finishing system (EIFS), or other exterior skin serves the same purpose, with IMPs as a viable alternative. The IMP system reduces wall assembly components, since IMPs act as a weather barrier, as well as an air and vapor barrier.
Horizontal application works well for low-height buildings or multi-story buildings where no intermediate steel structure is required, such as a typical office building. Often, designers prefer the horizontal orientation of the panels and seams for aesthetic reasons. For high, bay buildings greater than 4.5 m (15 ft) floor-to-floor dimension—approaching the span of economical application of light gauge metal framing—additional structure is required to connect the IMPs to the building, adding construction costs.
Vertically oriented IMPs can extend from the top of foundation wall to the building parapet, with the maximum panel length available on the market being 22 m (72 ft). Depending on the distance between horizontal connection points (span), intermediate horizontal connections (girts) may be required. These girts will attach to vertical building columns. The vertical application can have light gauge metal framing on the interior similar to the horizontal orientation, if the interior environment requires it.
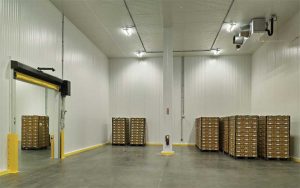
If an exposed metal surface on the building interior is appropriate, no light gauge framing is required. As a result, the building columns and secondary framing would be exposed, such as in a high bay warehouse application. This material efficiency makes the vertical orientation a viable option for interior functions in high bay spaces, especially when thermal environments, water resistance, and sanitation are important considerations. For sanitary conditions, exposed structure can be wrapped, or tube shapes specified.