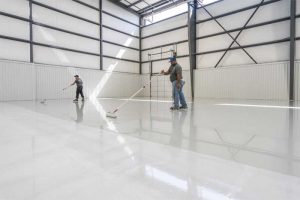
by Mark Thomas
Selection of flooring materials often starts with the preferred visual appeal based on the needs of the architect, interior designer, or owner. What materials would best meet the aesthetic needs: The warmth of hardwoods, the durability and decorative options of tile, or the economy and cleanliness of vinyl? Materials such as tile and sheet goods are typical options, but for many projects, high-performance coatings are a capable and often-desired alternative.
Few materials meet the combined benefits of coatings. The varied chemistries tailored within a complete system provide a seamless, easy-to-clean surface that withstands heavy traffic, impacts, and chemicals, all while offering anything from a utilitarian, industrial look to something fitting for a commercial setting.
However, selecting the right coatings and specifying the appropriate system can be more difficult than picking out a type of tile or vinyl. Some knowledge on the types of flooring, the common coating chemistries, as well as the appropriate performance characteristics of these systems can go a long way in helping construction professionals specify an enduring, aesthetically pleasing floor.
Flooring options
Before selecting a flooring system, it is important to first identify its performance requirements. Will it be exposed to foot traffic, wheeled carts, or something more abusive like a forklift? Will heavy items likely be dropped on it, or will there be aggressive cleaning techniques involving hot water spray, cleaning agents, or scrubbing? If the floor will be frequently wet or damp, what kind of skid-resistance is desired? Chemicals, fuels, lubricants, and other fluids often leak onto commercial floors: Is this exposure likely in the environment and how often will this happen?
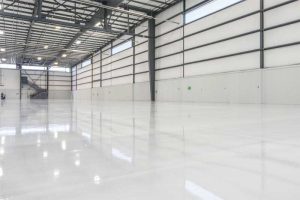
Once the exposure conditions and performance needs are identified, one of the following three basic types of high-performance flooring systems can be considered.
Thin-film flooring system
The most basic type of floor coating system is a thin-film floor, typically comprising two to three coats that will generally be between 380-1015 μm (15 to 40 mils) in total dry film thickness (DFT). This type of floor is available in a variety of colors, helping to achieve the desired aesthetic and visual requirements, while being easy to clean, especially because it is applied without the seams or grout lines found in vinyl or tile floors.
Thin-film systems can also be customized for additional skid and/or chemical resistance. Skid resistance can be tailored with the inclusion of aggregates or anti-slip particles for better traction, while chemical-resistant topcoat options make these systems a good choice for environments that will be exposed to cleaning chemicals or fuels on a regular basis. Material costs are lower for this type of floor and easy roller application also helps reduce labor costs.
The primary deficiency of a thin-film system is its resistance to point-load impacts, such as a dropped tool or other heavy item. The thinness and lack of aggregate reinforcement make a thin-film floor susceptible to impacts that not only damage the coating system, but also transfers the energy to the concrete substrate. This damage is repairable but might lead to ongoing maintenance and a visual ‘patch work,’ if they occur frequently.
Thin-film floor coating systems are often installed in commercial areas, such as offices, pedestrian corridors, vehicle bays, aircraft hangars, and production facilities.
Broadcast/laminate flooring system
If the performance requirements necessitate something more robust than a thin-film system, the next option would be a broadcast/laminate floor. These floors are usually installed at a nominal 3175 μm (125 mils) DFT and filled with aggregate. The aggregate in these systems not only helps achieve the higher thickness, but also reinforces the coating to make it more resistant to physical damage, such as abrasion and impact.
The popularity of this floor type has made installers adept at its installation. First, a coating layer is laid out by notched-squeegee after which an aggregate, or sometimes decorative flake or quartz, is broadcast into the liquid coating “to refusal,” meaning the coating cannot accept any more aggregate. After cure, loose aggregate is removed and the process is repeated providing what is referred to as a “double broadcast.” Next, these floor systems generally receive a grout-coat to help secure the uppermost aggregate. A finish coat is then often applied (depending on the needed service requirements) and can offer additional chemical resistance, color stability, or even abrasion resistance.