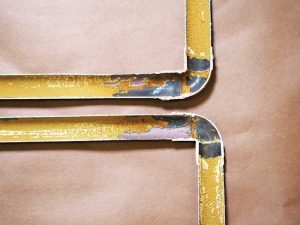
By Alan Humphreys PhD, PE, and Phillip Sharff, PE
Metal corrosion is an ever-present problem in the plumbing industry. Common piping materials such as copper, steel, and cast-iron are readily oxidized and thus undergo aqueous corrosion at a rate dependent on the corrosivity of the service environment.
When properly designed and installed, plumbing systems will provide many decades of problem-free service. Careful corrosion engineering management, including attention to details such as materials selection, fluid mechanics, water-chemistry control, protective coatings, cathodic protection, and suitable material corrosion allowance, should ensure these materials comfortably survive their design life. However, actions during the construction or renovation of a building can have unintended consequences that can dramatically reduce the service life of plumbing systems.
This article highlights some recent plumbing pipe failures caused by actions during construction or renovation and discusses methods to avoid such problems.
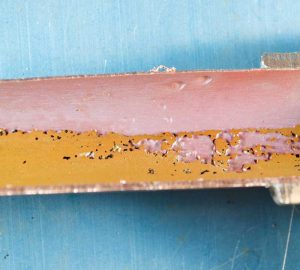
Erosion-corrosion of copper pipe
Seamless copper tubing conforming to ASTM B88—Standard Specification for Seamless Copper Water Tube— has been the most common material for small-diameter domestic water plumbing systems. This is because of its ease of installation, corrosion resistance, and competitive cost.
Clean copper surfaces are reactive with water, but oxide layers quickly form, which passivates the surface and retards further reaction. In addition, minerals in water can form insoluble scales such as carbonates, nitrates, and sulfates on tube interiors. This scale acts as a protective film to the copper surface, resulting in passivation of the pipe and a negligible rate of corrosion. The scaling potential of a water source is readily predicted from its chemistry, using indices such as the Langelier Saturation Index.
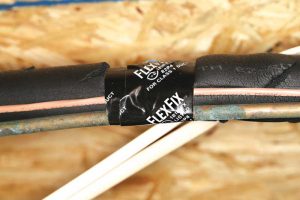
Mineral scale in copper tubing is chemically stable and under normal plumbing conditions would be expected to remain as a protective layer for the service life of the system. However, scale is mechanically weak and vulnerable to damage by turbulence due to high-water velocity or cavitation. This results in a sharp increase in the local corrosion rate where the protective scale has been removed—a mechanism known as erosion-corrosion. Plumbing codes typically limit the velocity of water flow in copper tubing to 1.5 to 3 m (5 to 10 ft) per second to avoid erosion-corrosion, and a mechanical engineer will design a plumbing system using pipe diameters sufficient to respect these limits. Unfortunately, if renovation work is carried out on a building, the original plumbing design is not always available, and modifications to the plumbing system can possibly alter the flow rate.
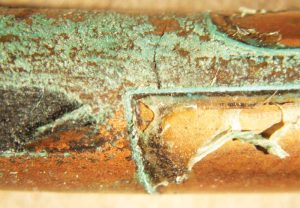
For example, the authors’ company recently worked on a project at a residential apartment building experiencing leaks in the domestic water system. This multi-story building had a recirculating domestic hot water system to allow rapid on-demand hot water at all locations within the building. During a renovation project, it was necessary to change the location of the basement piping, so the return line of this recirculation loop was re-piped. Unfortunately, the plumber replaced this line with 12.7 mm (0.5 in.) diameter copper pipe, whereas the original pipe was 19 mm (0.75 in.) diameter. The diameter change reduced the cross-sectional area of the return line by 55 percent, more than doubling fluid velocity, at a constant flow demand.
As a result, leaks began to occur immediately downstream of bends in the pipe, which is where turbulence can be problematic at high fluid velocities. On sectioning the leaking pipe samples in their laboratory to inspect the interior condition, the authors’ company found the protective scale was eroded away at the leak location and observed horseshoe-shaped pits oriented in the direction of the water flow (Photos 1 and 2). This internal condition is typical of erosion-corrosion.
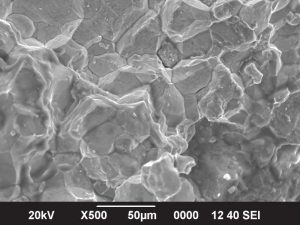
The authors’ company advised the building owner to replace the 12.7 mm (0.5 in.) diameter return pipe with the original 19 mm (0.75 in.) size. This failure demonstrated it is unwise to conduct modifications to a plumbing system without engineering review.