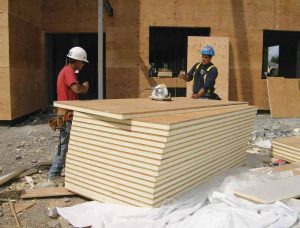
By Justin Koscher
The construction industry is one of the country’s largest energy consumers and contributors of greenhouse emissions. However, to mitigate its impact on the environment, it has set long-term sustainability targets and is heading toward decarbonization.
Efforts to decarbonize begin with reducing U.S. energy consumption, for which minimum performance standards and building energy codes are increasing in both scope and stringency. As a result, the use of energy-efficient materials and building practices is accelerating. This has led to the growing popularity and demand for high-performance buildings.
As building operations alone account for 30 percent of global final energy consumption, examining building envelope thermal performance is key to achieving energy efficiency and elevating overall building performance. Among the many energy drains, heating and air conditioning are two of the most resource-intensive activities that will test the performance of a building’s envelope (roof, walls, and windows). To prioritize thermal performance, specifiers are putting high-performance building materials to work, including polyisocyanurate (polyiso) insulation.
Examining the high-performance insulation solution
Polyiso is a closed-cell, rigid foam board insulation consisting of a thermoset foam core sandwiched between two durable facers. The material provides excellent resistance to heat gain and loss, offering one of the highest R-values per inch compared to other insulation options. Polyiso can be used in wall assemblies, roofing systems, and below-grade applications to create a well-insulated building envelope. Easy to handle, lightweight, and versatile, polyiso panels can be manufactured in a variety of thicknesses and dimensions to meet specific project needs. Since polyiso is a proven solution to address energy performance, it can be a key part of a specifier’s strategy to promote energy efficiency and sustainability in the built environment.
Types of polyiso
There are many different types of polyiso insulation boards based on the classification system in ASTM C1289, Standard Specification for Faced Rigid Cellular Polyisocyanurate Thermal Insulation Board. They are categorized based on the facers which range from foil facers, glass reinforced facers, coated glass facers, all glass facers, perlite board, cellulosic fiberboard, oriented strand board, plywood, and glass mat-faced gypsum board. Not only do facers contain the foam core during the production process, but they also add strength and dimensional stability to the finished polyiso board. Each facer has its own distinct properties, including reduced water absorption and water vapor permanence, restricted air movement, and increased thermal resistance. Further, some provide a drainage plane to shed water and others can add structural properties to wall and roof assemblies. Building teams can specify polyiso by facer type and other physical properties to align with their specific needs, which can help them achieve compliance with increasingly stringent building performance standards.