4 Ways to Track Equipment Easier—and Allocate Tools Back to the Job
0%
On its surface, equipment tracking is anything but sexy. It takes time, and resources, and doesn’t make a construction company any money at all. It doesn’t build structures, send bids, or make clients happy. But it’s one of those aspects of construction that, without it, the entire outfit runs inefficiently. There’s just too much waste and tail-chasing at stake to ignore it.
In fact, each job site loses about one day of labor per month because job site personnel are searching for tools. Likewise, the data that tool tracking offers is typically underutilized, meaning most companies that actually have an equipment tracking plan don’t even see their value. Worse yet, 57.5% of contractors express that they deal with the double entry of usage data and clerical errors.
But equipment management doesn’t have to be a complete anchor to your company’s growth. With the equipment tracking best practices listed below, your company can streamline the entire process, saving money and time while also keeping track of where your tools are, and which jobs they belong to.
Tips from Top Tool Trackers
The truth is that equipment management can be quite divisive. Equipment managers have a lot to do, like supply job sites with tools and consumables. They also have to come up with solutions and workarounds when things don’t go as planned, such as running to the big box stores for tools when they go missing or renting equipment when things break. They have other KPIs to make, as well, so they don’t have time to fool around with manual tool logging, making it tough to check tools in and out every day.
Similarly, financial staff have their own host of responsibilities. They’d rather not spend their time tracking down the equipment manager for the information they need about tools and equipment. And, when the equipment manager does provide the data, it’s not always correct. Accounting also doesn’t have the time to track down project managers and supers, but that’s often what they must do to locate the information they need. If they don’t, no one is tracking the small tool budget allocated to each project, resulting in lost profit potential.
Tool Tracking Solutions
Sure, the relationship between equipment and finance might not be as symbiotic as you might hope. But there are some best practices that contractors can implement to solve some of these challenges.
Inventory What You Have
The first step in healing the divide is inventorying the equipment and tools that the company already owns. After all, you can’t keep track of something you don’t know exists.
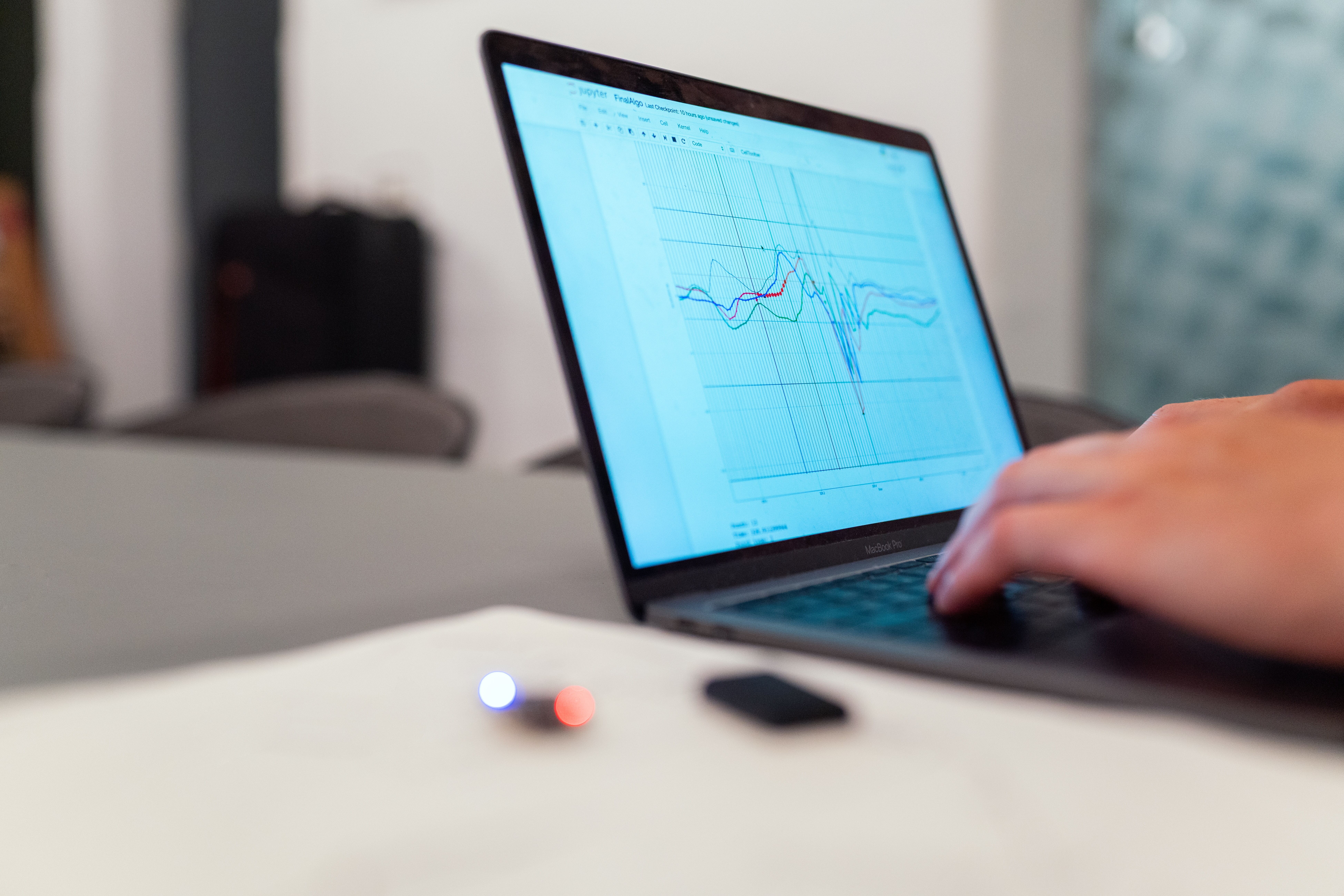
Paper recording and manual data entry are your enemies here. These inventory methods will get confusing, take too long, and aren’t easily trackable. Instead, utilize a tool tracking software that allows users to install tags on their tools for easy tracking. This will automatically enter the equipment into the system, allowing equipment managers and accounting staff to start working together right away.
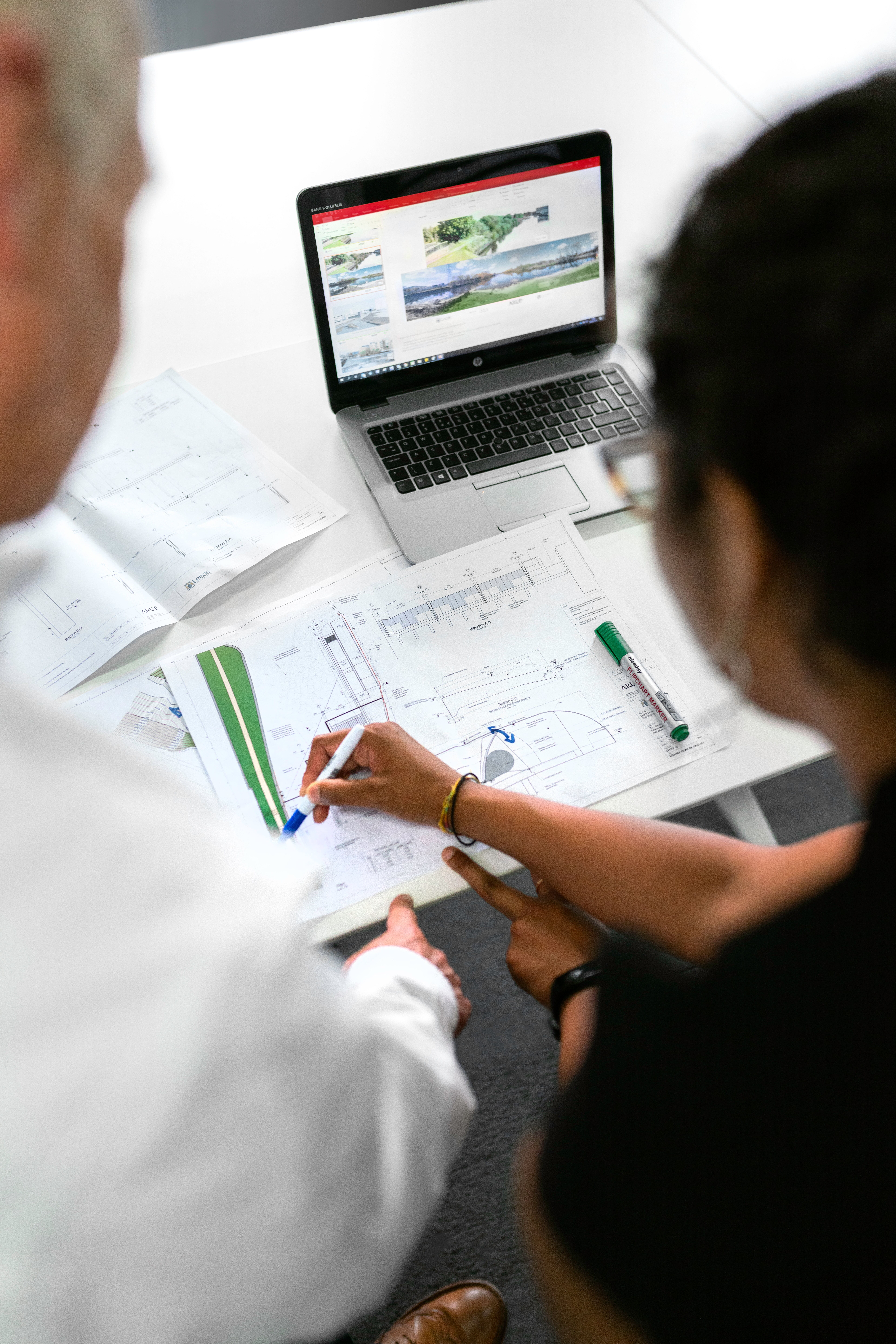
Assign Tools to Employees or Locations
One solution to the equipment management problem is to assign tools. There are a few ways to do this:
- Issue tools to each employee so they have their own tools to keep track of.
- Assign tools to employees at the beginning of their shifts or as they head to projects.
- Assign tools to a job site where employees can check them out.
Implementing these strategies requires a tracking system with tags (and a lockable room or cage if it’s a job site). As new tools are assigned, they’re tagged with a device that the equipment manager can scan and enter into the system. The employee is then responsible for the tool or piece of equipment, and the accounting staff can review the system entries to find the important data they need for their reports.
While there is an upfront cost for implementing such a system, this will save the contractor money in labor costs and tool purchases. This also allows for better tool maintenance tracking and can give employees an effective way of reporting issues with tools for faster service or replacement.
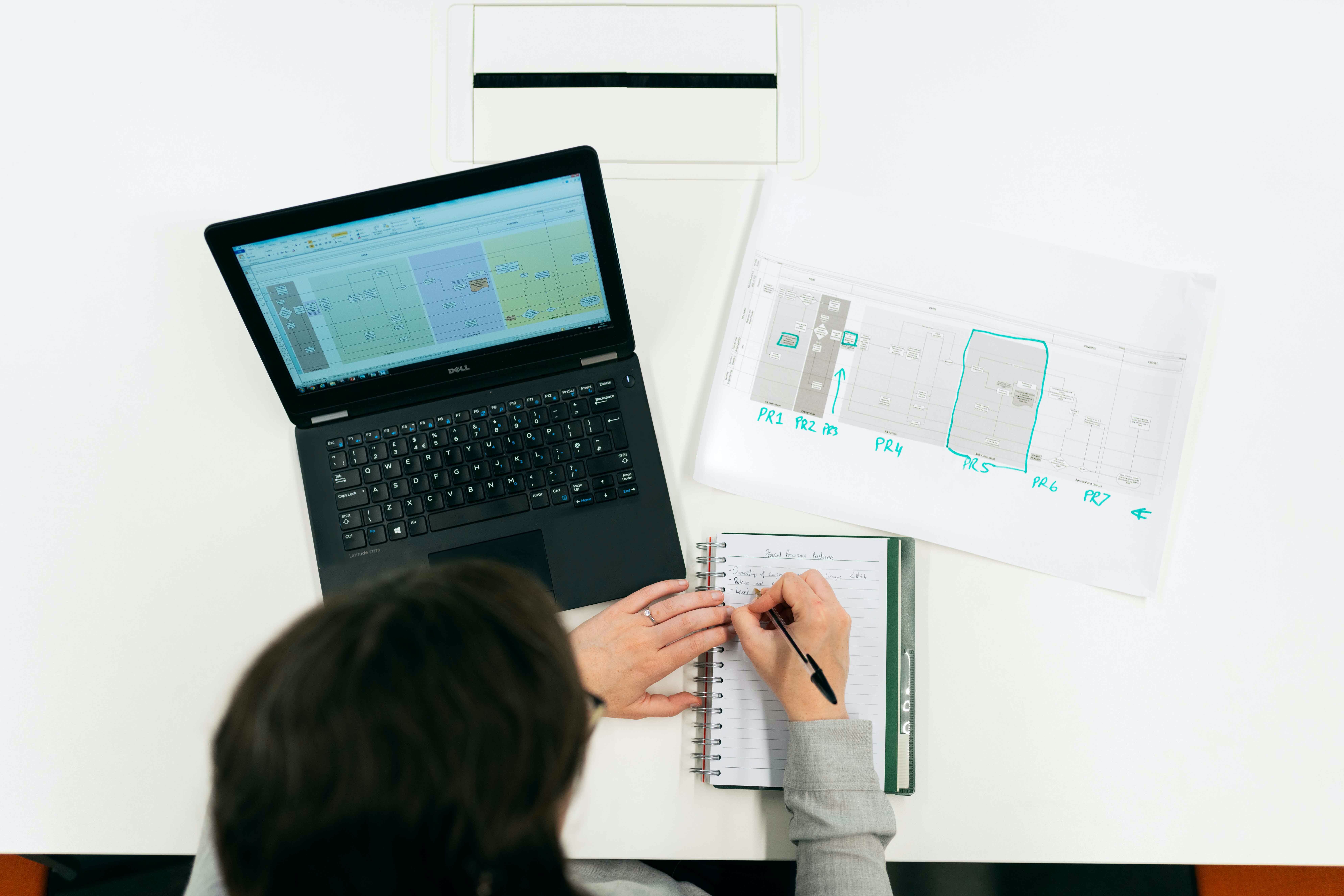
Connecting Your Office, Warehouse, and Field
Tool utilization, including how and where it's used, is an important part of a firm’s financial processes. But, tracking tools between the warehouse and field, and then appropriately allocating the associated costs in the back office is a lot of work. And it’s tough to be accurate, unless you connect the office, warehouse, and field with tool tracking software.
There are quite a few software options available that can track tools and the flow of data. Companies can implement these programs to increase utilization visibility across the board, allowing tool costs to be accounted properly throughout the current projects.
Reduce Double Entry
Any time data is recorded or entered twice is an opportunity to improve efficiency. Outdated manual entries take time to enter into a spreadsheet, slowing the equipment manager’s progress down over the course of a day. Worse yet, if data is recorded on paper, the process of collecting the paper and entering it into a digital tracking system is a nightmare. And you certainly need to account for errors.
Modern tool-tracking solutions do away with all of these frustrations. For example, rather than writing down inventory ID numbers, employee data, and project information, these newer systems allow employees to log in and scan their equipment, automatically logging all the information needed for the tool. That data is then available across multiple departments, eliminating the need for error-prone double entry.
Include Equipment on Invoices and Job Cost Reports
Once the data is in hand, a slew of new possibilities arise. In the past, incomplete or outdated data might not even be considered in an estimate, resulting in a phantom profit drain that no one accounted for. However, with tool tracking systems and a seamless flow of data between the warehouse, field, and office, tools and equipment can now be included in invoices and job cost reports.
Also, by tracking data over time, contractors can get a better idea of what their tool budgets look like. If they’re allocating too little, they can adjust their pricing. If they’re allocating too much, they might use these small budgets as bargaining chips in contractor negotiations. It also means putting together better, more accurate estimates for future projects with more stable profit margins.
The End Result? Equipment and Accounting Are Happy
Using those best practices, construction firms can keep both their equipment management staff and accounting staff in perfect harmony (more or less). It’s also a great way to save time in terms of administrative processes as well as labor, as you’ll be able to put manual data entry behind you. Don’t forget about the money you’ll save on tools, as well.
And if you’re looking for a software solution to move your equipment management needs forward, consider Hilti ON!Track, which integrates seamlessly with both Vista and Spectrum. Trimble is offering a number of incentives to current or new customers with Trimble Construction One.