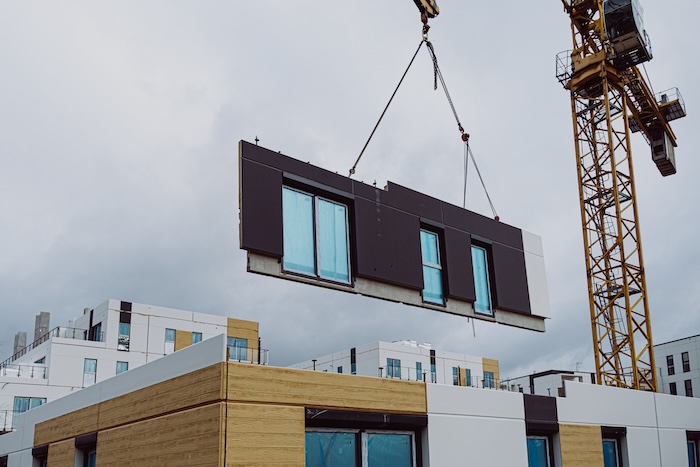
Prefab steel construction is transforming the building landscape with its innovative approach. This method utilizes prefabricated components, offering a modern alternative to traditional building practices.
Choosing between prefab steel and traditional construction involves matching the method to your project’s needs. This guide will clarify these options, providing a balanced view to inform your decision. You’ll discover the strengths and limitations of each method, leading to an informed decision that matches your building objectives.
Understanding The Options
Prefab Steel: A Closer Look
Prefab steel constructions utilize factory-made modules and panels, contrasting traditional scratch-built methods. Companies like Price Buildings provide the pre-made parts or structures the construction team assembles on-site. They have multiple advantages, such as:
1. Cost-Effectiveness
Prefab steel is generally more cost-effective due to its streamlined manufacturing and assembly processes, particularly for standardized designs. The bulk production of components leads to economies of scale, reducing the overall cost. The reduced construction time also lowers labor costs.
2. Faster Construction Times
The pre-made components, like those in Quonset building kits, allow for rapid assembly on-site, cutting down construction time. Commercial projects, often time-sensitive, benefit from this speed. Quickly erecting a building also mitigates the impact of unpredictable weather on construction timelines.
3. Durability and Low Maintenance
Prefab steel is known for its strength and durability, resisting environmental factors like wind, snow, and seismic activities. These buildings require minimal maintenance due to their resistance to rust, mold, and pests. They can remain functional and aesthetically pleasing for years.
4. Potential for Sustainability
For sustainable construction methods, prefab steel is the greener option. The materials used are often recyclable, and the precision in manufacturing leads to less waste during construction. The energy efficiency of steel buildings can be enhanced with proper insulation and design, contributing to a smaller carbon footprint.
However, prefab steel has its limitations:
1. Design Restrictions
While prefab steel buildings are versatile, they can somewhat limit design options. Custom designs are possible but might require additional planning and resources. This could sometimes compromise the architectural creativity of modular cabins, homes, and other structures.
2. Potential for Higher Upfront Costs
For specific projects, particularly those requiring customized designs, the initial costs of prefab steel can be higher. These costs stem from the need for specialized design, manufacturing, and sometimes transportation of components.
3. Availability of Specialized Labor and Contractors
Erecting prefab steel structures often requires workers with specialized skills in handling and assembling steel components. The availability of such skilled labor can vary by region, potentially affecting the construction timeline and costs.
Traditional Construction: A Solid Foundation
Traditional construction employs classic materials like brick, wood, and concrete. This method has evolved over centuries, showcasing benefits like:
1. Design Flexibility and Customization
Traditional construction methods offer unparalleled design flexibility. They allow for unique, customized architectural designs tailored to the needs and aesthetic preferences of the client. This flexibility enables the creation of structures with distinct character and style.
2. Potential for Higher Structural Strength
Traditional construction methods can offer substantial structural strength depending on the design and materials used. This factor makes them suitable for various applications, from residential homes to large commercial buildings.
3. Familiarity and Established Construction Practices
Architects, engineers, and builders are widely familiar with traditional construction methods. This familiarity streamlines the building process, potentially reducing errors and enhancing the overall quality of the build.
Traditional construction, however, has its drawbacks:
1. Longer Construction Times
Traditional building methods take time. Each phase, from laying the foundation to completing the interiors, requires significant time and labor. Factors like weather conditions and the design’s complexity may also affect the timeline.
2. Potentially Higher Costs Due to Material and Labor
Costs in traditional construction typically rise due to greater labor and material requirements. Custom designs and high-quality materials can further increase the price. Unexpected delays and changes during construction can also add to the overall budget.
3. Greater Environmental Impact in Some Cases
Traditional construction can have a significant environmental impact, though this varies based on the materials and practices used. This arises from the increased waste generation and the energy-demanding processes involved in construction. However, modern methods increasingly incorporate sustainable and recyclable materials.
Making The Right Choice
Choosing between prefab steel and traditional construction depends on several factors. Consider aspects like budget constraints, timeline requirements, and design aspirations. Each method has its unique benefits and potential drawbacks, impacting the overall outcome of your project.
Reflect on what matters most for your build. Are you looking for speed and efficiency, or is customization your priority? Maybe long-term sustainability and maintenance costs are your focus. Weighing these considerations will help you determine the most suitable construction method for your project, aligning practicality with your specific vision.
Conclusion
Prefab steel and traditional construction each have their unique strengths. The former excels in efficiency and sustainability, while the latter is renowned for its flexibility and potential for durability. Your decision will shape the course of your project, impacting everything from timelines to long-term satisfaction.
Consulting construction professionals can provide tailored advice for your project. With accurate information and expert guidance, you can select an option that perfectly fits your requirements, ensuring a reliable, effective, and gratifying project.