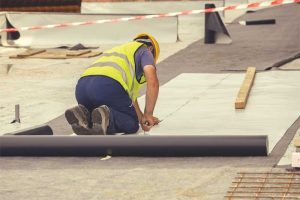
by William M. Woods and Daniel G. Gibbons, PE
Waterproofing below-grade portions of buildings has become increasingly important to owners as technological advancements and limited city space have pushed basements deeper into the ground and further into water tables.
Designers are utilizing subterranean building space for occupancy and other sensitive uses for which owners have little to zero tolerance for water intrusion. Engineered structural systems below grade also continue to advance. Waterproofing manufacturers publish detailed guidance for common conditions. Other project-specific or less common conditions are left to the designer. For most buildings, it is critical to maintain waterproofing integrity for the structural elements for many years.
Dewatering
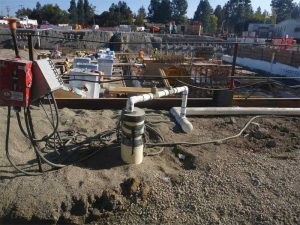
Images courtesy SGH
A foundation constructed within the water table must be dewatered during construction. Dewatering typically occurs at the onset of excavation and continues until 90 percent of the building dead weight is equal to the displaced water weight from the design high water table, and other work in the excavation no longer require dewatering. Project-specific factors, such as foundation tie-downs or soil conditions, can also affect dewatering.
Fractured shale and similarly stratified soils introduce dewatering challenges. Typical dewatering configurations consist of drilled well points that are designed to locally draw down water at each point (Figure 1). Collectively, these wells lower the subsurface water to below the excavation. These well points are more effective in porous, isotropic soils. In stratified soils, water lenses are confined between less permeable layers and may travel laterally. This water is often seen on shoring walls between exterior well points. While incidental water may not be a concern for the structural wall, waterproofing should not be applied over a wet surface. The overall effectiveness of the shoring in limiting leakage is best considered in the initial stages of design. When used as shoring, water cutoff walls provide greater resistance to moisture ingress when compared to wood lagging. Common below-grade waterproofing membranes require hot air welded seams, adhered laps, moisture-activated swelling, or a combination of these elements at transitions, all of which are sensitive to water during installation. In these conditions, the designer may consider additional barriers over the shoring wall and a perimeter base of wall trench to collect and convey water out of the excavation. A 15-mil plastic sheeting can be helpful for the field of the shoring wall, but special attention needs to be paid to tie-back heads and fasteners for the plastic and waterproofing.
Temporary or construction dewatering requirements for waterproofing substrates are seldom well defined early in the project. The geotechnical report that informs waterproofing strategies also sets requirements for dewatering. In many cases, these two elements diverge into independent design paths. Most dewatering configurations consider the structure and sufficiently manage water to prevent hydrostatic build-up behind walls or underneath the foundation.