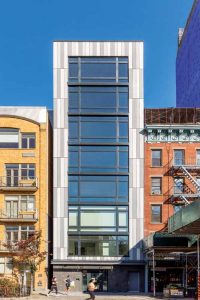
By Karine Galla
Lightweight cladding is gaining traction in the construction industry. With advancements in material science, the benefits of such cladding are increasing, and it is no longer necessary to use heavy materials such as masonry, concrete, metal panels, precast, porcelain, or even fiber cement to achieve the look of brick, wood, concrete, or metal. With the latest industry innovations, all these looks for building exteriors can be achieved using lightweight claddings. Aesthetics aside, sustainability and energy efficiency are major advantages, and installation is safer and easier for crews on site.
Cutting down on carbon
Carbon emissions from the building sector are significant, and they have an impact on the environment. In fact, according to the New Buildings Institute (NBI), “Building operations and construction-related activities are responsible for approximately 39% of humanity‘s global greenhouse gas (GHG) emissions. More than a fourth of those are embodied carbon emissions, those associated with the production of building materials, construction activities, operations, and end of life.”1 Therefore, both embodied and operational carbon are crucial considerations in today’s construction sphere.
Operational carbon is the amount of GHG emissions that are released during the in-use phase of a building. This includes the use, management, and maintenance of a product or building. In short, it takes into account the variety of carbon emission sources that are active throughout the operating period of a building.
How do lightweight cladding materials positively affect the carbon footprint? Starting from the top, lightweight materials are thinner, lighter, and take up less space during transit. This translates to less trucks overall and less gas expended to transport materials to the job site. By nature, lightweight materials also simply make for a lighter load to haul, which impacts fuel efficiency. For every 453-kg (1,000-lb) increase of vehicle weight, fuel economy drops by approximately 0.5 percent.2 Reducing the weight of the materials shipped across multiple truckloads can result in significantly reduced environmental impacts and diminished carbon emissions.
There are also key differences when it comes to the preparation of lightweight cladding materials compared to their heavier counterparts. Consider masonry cladding that requires heating and drying for extended periods of time in an 800-degree kiln. This consumes a great deal of energy. With lightweight cladding alternatives such as resin-cast brick, construction stakeholders can achieve the look of masonry, but in a much lighter-weight solution that takes a fraction of the energy to fabricate.
From an operational carbon perspective, lightweight cladding options that are installed as part of a fully integrated system deliver even greater savings. Innovative systems that combine lightweight, high-performance cladding, superior air and weather barriers, and excellent thermal properties via continuous exterior insulation save on energy consumption, generating additional cost savings for owners. Therefore, specifiers can choose systems that meet the most stringent building code standards, as well as those that meet requirements for an NFPA 285-compliant assembly.