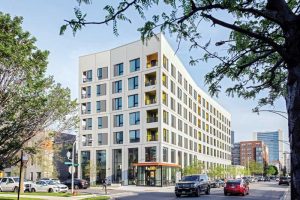
By Emily Lorenz, PE
With the signing of the Infrastructure Investment and Jobs Act (IIJA)1 and the Inflation Reduction Act (IRA),2 federal funds for infrastructure construction and low-embodied carbon materials will soon be entering the construction pipeline.
An environmental product declaration (EPD) discloses the environmental impacts of a construction material or product over a portion of, or all of, its lifetime. This makes it possible to understand the relative impact of different products and materials. EPDs allow a manufacturer to be transparent with interested parties, such as architects, designers, and specifiers, about its products’ environmental performance.
Precast concrete is in a unique position because precast concrete projects are built to last longer than other construction materials. This means considerations other than cradle-to-gate environmental impacts typically reported in an EPD should be evaluated. Cradle-to-gate encompasses the production stage of the lifecycle stage, or modules A1 through A3 (see “Lifecycle stages” sidebar on page 30). Frequently, the overall lifespan of a building must be considered to understand the full environmental impacts of design decisions. Thus, a full lifecycle assessment (LCA) of a building is necessary.
From voluntary transparency to government mandate
Initial awareness of sustainable design and construction in the U.S. can be attributed to the Leadership in Energy and Environmental Design (LEED) rating system, embraced primarily by architects in the design and construction communities. Other voluntary programs have been launched over the last 15 to 20 years, such as the Green Building Initiative’s (GBI’s) Green Globes and the International Passive House Association (iPHA), but none have matched the reach and influence of the LEED rating system.
When the construction industry first started responding to requests for the environmental impact of products, the requests were typically coming from architects wanting to know the recycled, biobased, or regional material content of products. This information was used to document requirements in the LEED rating system, then used to achieve points and ultimately a rating of the final structure.
As the LEED rating system evolved, submittal requests expanded to include requests for EPDs. Through this voluntary program, manufacturers were encouraged to create EPDs in order to transparently report the potential environmental impacts of their products. Manufacturers were further encouraged to produce plant-specific EPDs by rewarding their “value” as twice than that of an industry average EPD toward the number of points or products required. (See more on industry-average versus plant-specific average in the “EPD Basics” section).