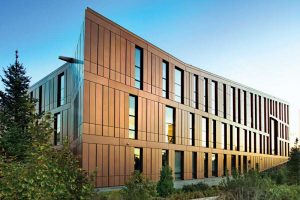
By Tammy Schroeder
Anodizing protects and enhances aluminum cladding in exterior and interior applications. Installed on a building exterior, anodized wall panels must withstand continuous exposure to direct sunlight’s ultraviolet (UV) radiation, precipitation including salt spray, and pollution and other climatic conditions of the project’s location. For interiors, anodize cladding often is specified for its consistent durability in holding up to daily wear, bumps, and scratches from people within the building.
The anodize process
Unlike architectural painted coatings that are applied on top of a material’s surface, anodizing is a finish produced by electrochemically controlling, accelerating, and enhancing oxidation. Anodize is an integral part of the aluminum substrate.
Architectural aluminum anodize typically involves a two-step electrolytic process where the aluminum material is submerged in a series of tanks. After the material is cleaned from grease, oil, dirt, and other contaminants, the first step is placing it into a tank containing an acid and water solution.
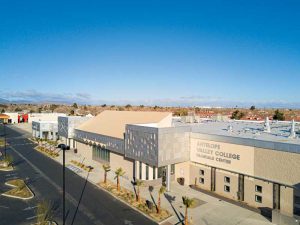
The acid dissolves a thin layer on the surface of the aluminum which allows it to develop a smooth uniform finish. Up until the early 2000s, anodize mainly was produced through a conventional, caustic etch process which relied on an aggressive alkaline chemical. Now, most modern finishing facilities rely on an acid etch fluoride-based ionic chemistry. The acid etch process takes approximately 15 minutes and removes only 0.01 kg (0.002 lb) per 0.09 m2 (1 sf) compared to the caustic etch, which took up to 80 percent longer and removed 90 percent more aluminum.
The anodize tank is charged with an electrical current which causes natural oxide to form on the aluminum’s surface. This heavy oxide film has a controlled, uniform thickness, and an extremely hard surface which protects the metal substrate from deterioration. In fact, the hardness of anodize is comparable to a sapphire, the second-hardest substance on Earth. This material property imparts the finish with excellent resistance to wear and abrasion, making anodize an optimal finish choice for aluminum cladding systems.
To minimize potential inconsistencies, one should specify 5005 aluminum alloy, in anodize quality, for flat sheet as well as consider sourcing all the metal from one lot of material from a single supplier. When anodizing flat sheet for exterior wall cladding panels, the aluminum needs to be a minimum thickness of 1 mm (0.04 in.).
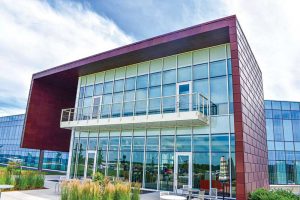
Clear anodize results after the material has gone through the cleaning, etching, and anodizing process. The result highlights the aluminum’s natural silver color. If other metallic tones are specified, the aluminum continues an additional step, where the anodized aluminum is immersed in the electrolytic color tank(s).
Are you doing in person presentations?
are you looking for presentations on anodizing for exterior walls, or for a particular panel system?
I’ll start by saying that Linetec is a great company that willingly offers expert advice, and provides finishing services second to none. I thank Linetec (particularly Tammy Schroeder) for the many valuable articles it has provided, and for the wealth of information on its website.
But I’ve always been puzzled by Linetec’s use of terms related to anodizing. When talking with their representatives, I often would suggest changes, but they never responded. Of course, the people who deal with clients usually can’t make changes on their own, so in June of 2010, I sent an email the vice president of sales and marketing. In it, I explained that “Anodize is a verb, it is not a noun. To anodize is to apply a protective coating. Anodizing is either a verb, ‘We are anodizing the metal’ or a gerund that is the name of the process, ‘Let’s talk about anodizing.'” I also noted other instances where Linetec’s literature or website used terms incorrectly. I don’t recall receiving a response.
More recently, while serving on the Construction Specifier’s Editorial Advisory Board, I reviewed an article titled “Maintaining and Protecting Architectural Aluminum Finishes,” which appeared in the February 2010 issue of the Construction Specifier. In my comments, I changed “anodize” to “anodizing” in several locations, and to “anodized” in at least one location. It was interesting to see that in the published article, virtually all of my other suggestions and comments were addressed, yet the incorrect use of “anodize” remained.
If this were an industry trend, I might care less, but I’ve looked at information about anodizing published by several other anodizing companies, and they use the terms correctly – even the oddly-named “US Anodize.”
I know, some will say, “What’s the big deal? It’s only a word!” But in the world of specifications and construction documents, we must be consistent, and we must use defined words as they are defined. I don’t know why Linetec insists on its use of these words in their unusual way, but at least they are consistent. I can imagine a time when someone new to the company was familiar with the word “paint” – which can be either a noun or a verb – but not “anodize” – and might have thought “anodize” would be used in the same way as “paint.” I doubt that specifiers have been using “anodize” as a noun; I wonder how many cringe just a bit when they see it used that way.