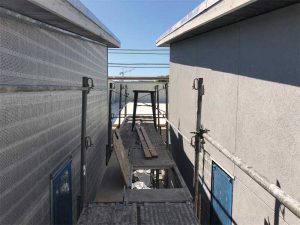
by Peter Barrett
One of the most reliable ways of keeping the exterior walls dry or allowing them to dry out when they do get wet is to construct an assembly with an outer protective shell, also known as a rainscreen. The assembly comprises, at minimum, an outer layer, a protected inner layer, and a cavity between them sufficient for the passive removal of liquid and water vapor.
Although the term “rainscreen” emerged in the 1960s, earlier examples date back to the 19th century. They are effective at managing moisture and provide exceptional opportunities for energy-efficient performance through continuous insulation (ci) and reducing thermal bridging. According to the Green Built Alliance, rainscreens are one of the best ways to increase durability and prevent water damage to buildings.
Rainscreen walls have had a few different definitions over the years. In the past, it generally referred to a façade material. The term now typically defines an entire system supported by the exterior wall and designed with products and details that assist in creating pressure-equalized and ventilated systems. Ultimately, a rainscreen is the protective exterior barrier wall system. Some rainscreens and components are engineered to function as a complete system: the material, the type of channel and clip arrangement used to fasten the rainscreen veneer, the dimension of the air gap, the air- and water-resistive barrier, and flashings.
Building researchers and scientists through the 1960s and 1970s tested and validated open rainscreen systems as well as simple vented and drained systems. The American Architectural Manufacturers Association (AAMA) published the first guide for pressure-equalizing designs in 1971. Today, while research and testing on rainscreens continues, there is a growing initiative to standardize rainscreen specifications and criteria.
To understand the importance of industry standardization, let us review the role of a rainscreen in detail.
Rainscreen performance
One of the most important aspects of building enclosure durability is moisture control. Since many wall cladding systems are not watertight, managing water, as either vapor or liquid, is a critical design goal. The issue is not if water will penetrate, but how to handle the water when it does.
The three major categories of commercial wall assemblies (mass walls, barrier walls, and drained or screened walls) handle moisture differently. Drained or screened walls are the most popular assemblies and differ from mass and barrier walls in that they contain an air space behind the cladding. Moisture that gets past the cladding is stopped by a water-resistive barrier (WRB) and drained away from the building, and moisture is not drawn into the interior structural assembly.
A rainscreen should be viewed as a building envelope protective mechanism, adding reserve to the ability to manage moisture. Contrary to popular belief, the primary function is not to act as a barrier against water penetration—that is the WRB’s role. A rainscreen is designed to limit the amount of water that could potentially come into contact with the primary building envelope’s moisture barrier. This reduces the likelihood of water entering the wall assembly by resisting the five forces that can drive moisture into buildings. Those forces are kinetic energy, gravity, capillary action, surface tension, and pressure gradients.
Rainscreens add two key performance features to a wall system: drainage and ventilation. The drainage space allows the passage of bulk water to the exterior. Ventilation provides enhanced capacity to dry and moderate humidity within the cavity.
All rainscreen systems rely on the air gap between the cladding and exterior wall to prevent water from penetrating the structural wall assembly. A rainscreen typically consists of five components:
- exterior cladding (with or without open joints);
- ventilation and drainage cavity (air gap);
- WRB;
- insulation; and
- structure.