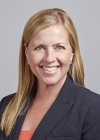
The COVID-19 pandemic is impacting engineering and construction businesses of all types and sizes in the U.S. Sector companies are facing many challenges, from delayed projects to difficulties procuring materials and equipment. Leading contractors are responding by accelerating digital implementation, automation, and increased use of prefabrication and modularization, which will likely help offset the impact on construction activities. This article explores the impact of the pandemic on the sector and the approaches sector companies could take to respond to and recover from the crisis.
Although construction is one of the few sectors that seems to have escaped the full brunt of the COVID-19 crisis, sector companies face multiple short-to-medium-term challenges. These include an increase in project delays/projects being put on hold, difficulty obtaining permits for projects, stalled construction, rise in project cancellations, anticipated increase in claims and litigation, and difficulty in procuring materials and equipment such as structural steel and glass from Asia. As a result, design firms and contractors are seeing a slowdown in activity on projects, which could extend to projects that are likely to start in the near-term. The path forward includes dialing up digital assets to ensure a safe and productive job site and focus on prefabrication and modularization.
Technology Mitigates Impact
Increasing project visibility, improving workflow, and streamlining scheduling activities are more important than ever due to the pandemic. Digital technologies are increasingly becoming a must-have for contractors as they have the potential to help improve productivity, reduce costs, and meet project timelines (see graphic). As a result, many contractors are focusing on these technologies as one of their major strategies to respond and recover from this crisis.
[For ENR’s latest coverage of the impacts of the COVID-19 pandemic, click here]
From connected job sites to digital supply chains, many contractors are calibrating various technologies that can transform their workplace and bring greater efficiencies. As the pandemic has brought workers’ safety to the forefront, AI-based solutions offered by technology firms are helping companies create a safe working environment. For instance, Guardhat wearable devices have sensors and RFID readers to detect/scan PPE, applying real-time location of the device to intelligently alert the wearer to use the right PPE for that location/zone. Sensors and AI algorithms on wearable devices detect falls and man-down situations and take quick action in real time such as alerting nearby workers, dispatching emergency response teams, and capturing biometrics. The crisis is likely to act as a catalyst for construction companies to accelerate the adoption of digital technologies:
Job Site Technologies
Keeping construction projects moving during the pandemic requires a complete rethinking of job site processes, and new technologies are emerging to help. A leading national contractor has deployed a custom-designed wearable IoT tag to remind workers to maintain social distancing and provide contact-tracing information for job sites. Some contractors are using social distancing automation, which includes automatic detection and notification to crowding workers with patterned vibration and visual message if a cluster of people is too close. In addition, many companies are leveraging virtual and remote monitoring of on-site workers to ensure compliance with the safety standards.
Connected Construction
Contractors are also increasing the use of cloud services as well as digital collaboration tools to ensure job sites are connected, which makes remote management and collaboration easier. IoT is enabling intelligent asset management, including inventory management and equipment monitoring and repair.
Drones and Robotics
Many construction companies are using robots and autonomous rovers to reduce the need for humans to conduct site inspections and to automate repetitive tasks like bricklaying. This addresses the challenge of reduced labor at construction sites amidst the lockdown.
The pandemic is pushing contractors to increasingly use drones for remote site monitoring, surveillance, and inspection of construction projects. Drones are enabling construction teams to have a detailed overhead view of job sites, materials, machinery and people. Drones record images and videos which help optimize grading plans and operations to identify differences between as-designed and as-built site plans.
Digital Twins
5D BIM, augmented reality and virtual reality are supporting seamless planning and design of projects without being physically present at job sites, mitigating the disruption in construction. These technologies help reduce costs incurred during project planning and speeding up development timelines.
The pandemic will likely push firms toward modularization and prefabrication of components
Contractors are moving towards modularization and prefabrication of components, from design to installation, to mitigate the impact to their bottom lines. Many construction companies have already begun leveraging modularization and prefabrication to drive efficiencies and overcome schedule overruns. As the crisis continues to disrupt construction activity, contractors are adding modular assembly yards—strategically located sites for fabrication and assembling building elements that can then be transferred to a construction site for rapid assembly.
An enhanced focus on worker safety is likely to help accelerate the sector’s move towards these offsite construction methods. The assembly-line efficiency and controlled environment of a construction “factory floor” can bring cost savings with higher efficiencies in labor productivity and shortened project schedules. Specifically, modularization is expected to improve contractors' productivity and margins, especially during a time when on-site labor needs to be reduced to the bare minimum. Moreover, prefabricated construction is enabling work in a controlled environment, which helps control costs and mitigate risks.
In addition to reducing labor costs, modularization is driving improvements in quality and shortening project schedules, which will be critical during the pandemic as schedules overruns are likely to increase significantly. Along with modularization and prefabrication, 3D printing is helping contractors to develop innovative designs and create superior structures that help improve the construction schedule.
The Way Forward
The engineering and construction sector is likely to experience a speedy recovery in 2021 as sector companies are expected to experience pent-up demand in late 2020 and early 2021. In particular, infrastructure and public utility projects could possibly see a sharp rebound, driven by government spending support and increased funding/liquidity.
Digital technologies, modularization and prefabrication remain the critical areas business leaders must focus on to recover from the crisis. Sector leaders could consider if the crisis can be used as a catalyst to rethink how work is done and to accelerate the adoption of digital capabilities. The extent of digital adoption by firms is likely to play a pivotal role in their ability to recover in the coming months. Increasing the use of modularization and prefabrication could also be a way forward for firms as these off-site construction methods help offset impacts on construction activities. To remain competitive, sector firms need to accelerate their digital transformation and use of innovative construction methods to address the changes brought on by COVID-19 pandemic.
Michelle Meisels is a principal in Deloitte Consulting’s technology practice and leads its Engineering & Construction practice. Michelle has more than 20 years of consulting experience with a focus on leading large, often global, finance and information technology transformation programs by leveraging technology. She helps clients integrate best-in-class technologies with organizational and process standard practices to achieve both qualitative and quantitative benefits. While Michelle has served clients across many industries, her primary focus has served engineering and construction companies that include AECOM, URS, Earth Tech, Worley Parsons, and MWH. She was born and raised in Southern California and graduated from UCLA.
Post a comment to this article
Report Abusive Comment